
Value Driven Maintenance is a financial modelling method to pick maintenance process improvements. Used alone VDM gives you a “starry-eyed” view of maintenance savings. Once you combine VDM with Plant Wellness Way system-of-reliability analysis you get practical solutions.
Keywords: project risk management, Value Driven Maintenance, business process improvement
Value Driven Maintenance (VDM) is a corporate management philosophy for getting the most worth from a company’s maintenance efforts. VDM focuses on maximizing the value gained by the maintenance group through optimizing four factors it can influence: asset availability, control of costs, effectiveness of resource allocation, and the organization’s occupational health, safety and environment (SHE) performance. The aim of VDM is to turn Figure 1 into Figure 2 by finding the most profitable ways to minimize equipment failures, prevent the waste of resources, and eliminate operating and maintenance process losses so maximum value is gained from a process.
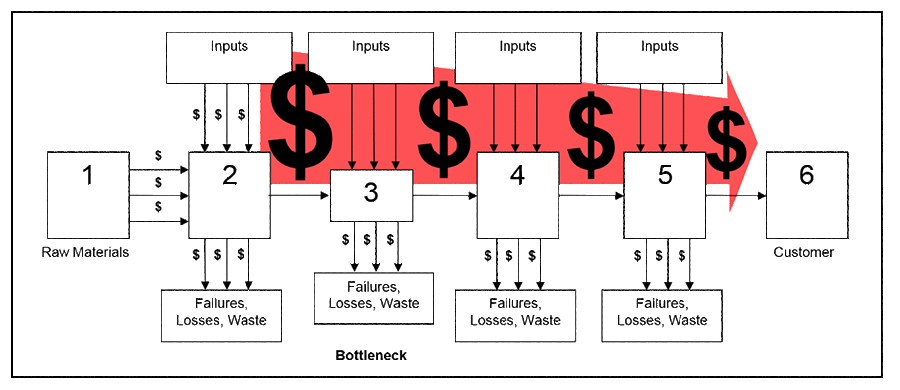
A formula is used to gauge the current financial worth of the four factors that maintenance can influence. The VDM formula sums the net present value across the years to calculate today’s value of future maintenance done. By changing how maintenance is done the value changes. This gives you a way to identify in advance which maintenance strategies and actions will generate the most worth. The VDM formula is:
PVmaintenance = Σ {FSHE,t x (CFAU,t + CFCC,t + CFRA,t + CFSHE,t) / (1+r)t}
PVmaintenance = present value potential of maintenance
FSHE,t = SHE factor in year t (% compliance with Safety, Health & Environment Compliance)
CFAU,t = future free cash flow in year t from Asset Utilization
CFCC,t = future free cash flow in year t from Cost Control
CFRA,t = future free cash flow in year t from Resource Allocation
CFSHE,t = future free cash flow in year t from SHE
r = Discount rate for year t
A weakness with VDM is that it does not have a systematic way to arrive at useful changes, instead it requires suggestions and guesses to be put forward for review. By combining Plant Wellness Way (PWW) “system of reliability” modelling with Value Driven Maintenance you can find the most profit maximizing asset management strategies, cost reduction plans, resource optimization, and SHE incident controls to use.
As you find new PWW value-driven solutions, then choosing the best asset management, cost control, resource management and Safety, Health and Environment practices and methods is a matter of using the VDM formula to spot the most value-bringing choices.
The combined PWW and VDM analysis takes each maintenance and operations process used in an organization and looks at each of its process steps in detail. In each step, first analyse how to maximize asset availability, then you go back through the process again to find how to reduce its costs, then back through again for how to allocate the company’s resources most effectively, and lastly for how to improve occupational health, safety, and environment performance. At the end of the analysis, you will get dozens, perhaps even hundreds, of improvement proposals to gain more value from each of your processes.
To reduce the number of proposals down to those you will cost in detail with the VDM formula you use a simple project selection method, like the one in Table 1.
Another weakness of VDM is that it is not a risk based methodology. VDM makes “everything look rosy” and you never realize the impact of an improvement project’s failure to the organization. Using VDM alone does not fit well in an ISO 55001 enterprise asset management system.
Here again Plant Wellness Way EAM system of reliability modelling protects you against unknown risk because each VDM “improvement” is tested for its impact on process reliability. If you have a
valuable change that is also a high business risk you proactively spot the problems and act to eliminate project risk so you are more certain to get the full potential value of your improvements. Every Plant Wellness Way Consultant knows how to do system-of-reliability modelling to protect and profit their clients’ business. Give one a call when you want to find the best improvements for big maintenance success.
Mike Sondalini
Leave a Reply