
Equipment and machinery reliability grows as machines are made more accurately and components kept in more perfect condition. Finesse and refinement practised on equipment parts extends equipment life by months, sometimes many months. Once you reach superb precision and work quality control your reliability growth bounds forward by years at a time. Conversely, when assembly accuracy is poor or parts’ environments are degraded you lose reliability at a rate of years at a time. In fact, the rate at which you lose reliability when component health is lost is as if you threw your machine from a cliff. Many industrial companies blindly commit industrial suicide daily by leaping off ‘reliability cliffs’.
Keywords: reliability growth, reliability improvement, component life extension
Table 1 is famous in the world of equipment maintenance and reliability. It shows the results found by the British Hydromechanics Research Association from a three-year controlled ‘field’ study of 117 hydraulic machines (injection molding, machine tools, material handling, mobile equipment (earth moving, etc.), marine hydraulics, and test stands) with the purpose of correlating hydraulic fluid cleanliness to machine breakdown frequency. Using a life factor = 1 achieved with ISO 4406 18/16 level of particle contamination; you can observe how operating life falls once hydraulic oil contamination gets above that value. It is plainly clear that oil dirty with particulates rapidly fails hydraulic systems.
Oil Particulate Contamination Reliability Cliff
When you put the information in Table 1 onto the simple graph of Figure 1 you see a ‘reliability cliff’. ‘Reliability cliffs’ show up in graphs and plots of equipment service life as rapid falls into reliability disaster.
Metal Fatigue Reliability Cliff
Figure 2 is a fatigue curve for a ferrous metal. Standard samples were put through laboratory fatigue tests during which the specimens were cycled at known stress levels. The cycles to failure were charted against applied stress, producing the plot shown in Figure 2. When the data from Figure 2 is graphed on the linear scales of Figure 3 another ‘reliability cliff’ appears.
Shaft Misalignment Reliability Cliff
Figure 4 is from the Shaft Alignment Handbook by John Piotrowski. It is a plot of the typical operating lifespan of rotating machinery being subjected to various amounts of misalignment. The data is based on a large number of case studies where shaft misalignment was found to be the root cause of rotating equipment breakdown. Graph the bottom curve of the failure zone in Figure 4 and the ‘reliability cliff’ of Figure 5 reveals itself.
Roller Bearing Internal Clearance Reliability Cliff
Figure 6 is from FAG Bearings research. It shows the ratio of 6310 ball bearing service life compared to design life verses bearing internal clearance (25.4 micron = 0.001”). It presents the effect of altering ball bearing internal clearance on operating bearing lifespan. You can easily see the ‘reliability cliff’ that it contains. For the ball bearing a small preload actually improves service lifetime above designed life but, as Figure 7 highlights, once that point is passed you fall off the ‘reliability cliff into rapid bearing failure.
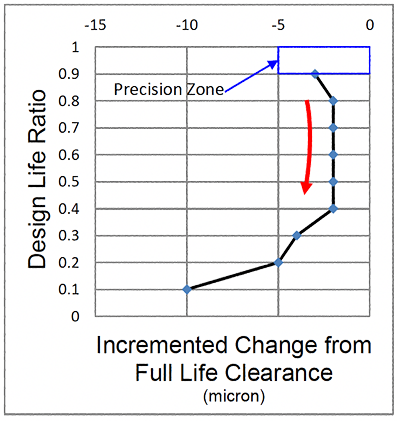
Figure 8 was derived from the ball bearing life curve by asking ‘how many microns change destroy each 10% of bearing life?’ Starting at the full life preload of -20 micron, the change in clearance for each 10% loss of life was gauged and then graphed in Figure 8. Another ‘reliability cliff’ appeared (an abyss actually).
Getting roller bearing clearance right is part of first assembly. The machine designer specifies suitable manufacturing sizes and tolerances for optimum new assembly fits. Keeping internal clearances right, i.e. within 10μm of perfect, during operation and rebuild is enormously harder. You must bar component distortion; prevent temperature rise (and fall); stop fatigue stress cycling—you must control all operating conditions masterly. It is hard to do, but vital.
Reach Mechanical Equipment Standards that Cause Reliability
The seven major mechanical health issues noted in Figure 9 need to be mastered collectively to get highly reliable machines. Each requirement has a precipice that will kill your operation. Leave one go out of control and world class reliability is unachievable. Step out of the precision zone with any of them and you can lose reliability so fast that seems as if you jumped off a cliff.
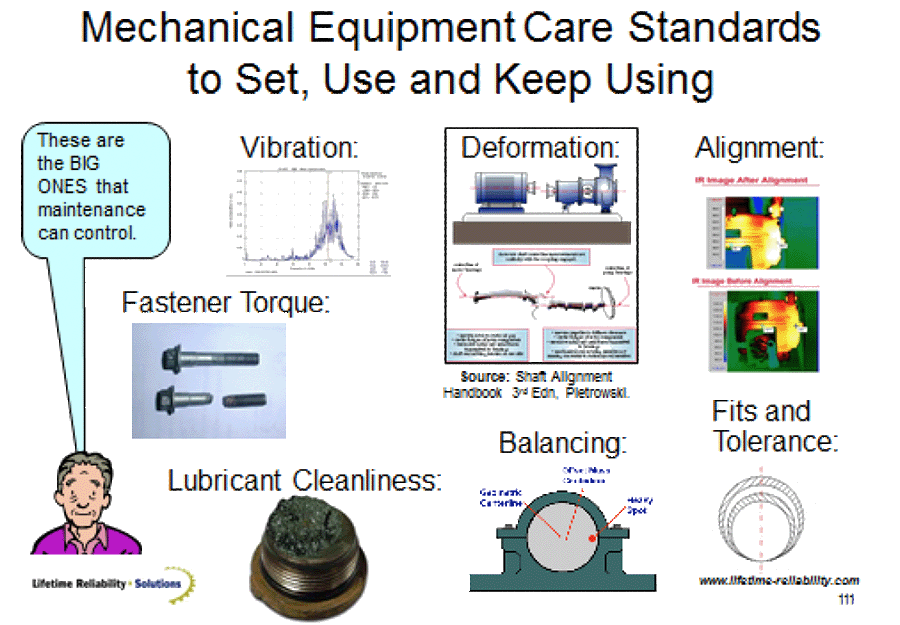
Machinery reliability is a human creation. You make reliability; it cannot happen by itself. Reliability success is a sculpture. There is but one way to make machines reliable: their parts must first be reliable. High machine reliability needs life cycle processes and supply chains that deliver dependable precision quality to working parts. The health of your parts produces the reliability of your machines. The way from the reliability cliffs starts by setting parts and work quality targets like in Figure 10. Meet the quality targets concurrently and you make reliability.
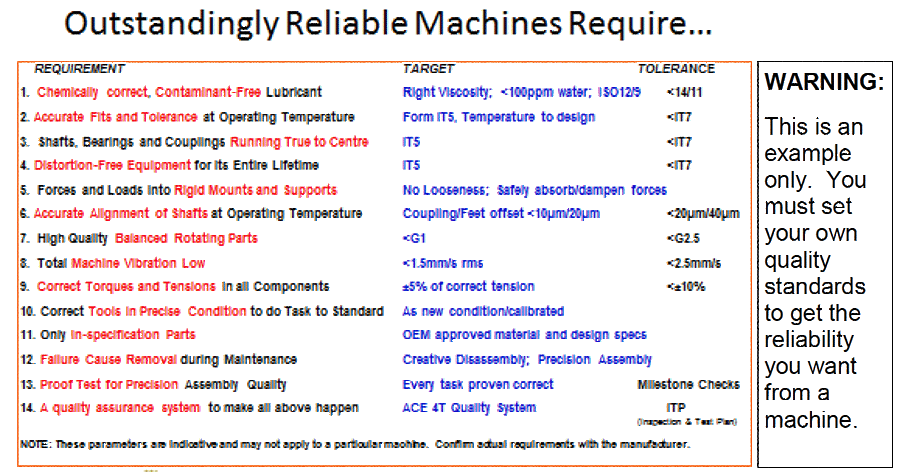
Live Reliability Life to the Full in the Precision Zone
Life is great at the top of the reliability cliffs. The view is magnificent. The air is clear and fresh. You get the sunshine from dawn to dusk. You have time and money to enjoy yourself and pursue happiness. But take one pace too far in the wrong direction and happiness ends forever.
Reliability success is often said to be a journey, but it is the wrong metaphor—reliability success is a climb! Reliability is a step change. Either you have reliability, or you are doing one of the following: 1) constantly correcting problems, or 2) always fixing broken things. World class machinery reliability is only found in the peaks of machinery Precision Zones. It cannot survive anywhere else: long-lived, trouble-free reliability is a mountainous climb to where lasting precision quality lives!
Industrial Suicide Continues Everyday Everywhere
All our machinery reliability problems, and all the answers to prevent them, have been known since the 1970’s (otherwise you cannot build reliable rockets); most were known prior the 1950’s (otherwise you cannot build reliable planes); the great majority are from the 1930’s (otherwise you cannot build reliable cars). Many Internet queries were made in researching this article. There are mountains of sound advice with correct solutions at hundreds of specialist websites that advise readers how to solve every equipment reliability problem. Everything necessary to have astoundingly reliable plant and machinery is available to us all. Yet, even with all the answers, even after decades of knowing what are the right things to do for sure machinery health; most industrial operations, utilities, production plants and facilities still suffer poor availability, low equipment reliability, expensive maintenance and high operating costs.
After such a long time of knowing the right reliability answers there is now an elephant-in-the-room question: Why do so many companies still commit industrial suicide every day by throwing themselves off reliability cliffs? Mass suicide is uncommon in history. At Wikipedia only thirteen mass suicide episodes are listed for the past 2,200 years1. Yet mass reliability suicide happens in industry world-wide every day. What causes so many companies to make their machines fail and consequently destroy their businesses and future livelihoods? Does the plague of self-induced machinery failures, even though we know exactly how to stop them all, mean we are mad? Is there a shared insanity causing the reliability suicide epidemic?
There is a craziness that continues to destroy equipment in industrial operations. Its causes are unclear; but it exists—it happens every day everywhere, at great loss to us all. Whether the daftness is because of company structures, in business processes, in society, caused by government, or it is because of our education systems (or some combination of all; perhaps even a thing unknown) is not evident. Stopping whatever lunacy is making so many of us jump off reliability cliffs is now the most important research needed. Until we have explored, understood and eliminate reliability suicide, our machines will continue to die on the reliability cliffs.
My best regards to you,
Mike Sondalini
Lifetime Reliability Solutions HQ
Leave a Reply