
First parts fail, then machines stop! If its parts don’t break your machines and equipment will always be reliable
Physics-of-Failure microstructure science explains why components fail, and why they get failed during service life. Understanding Physics-of-Failure is foundational to the Plant Wellness Way EAM methodology
Slide 11 – Physics-of-Failure Microstructure Science Explains the Failure of All Parts and the Breakdown of All Machinery and Equipment
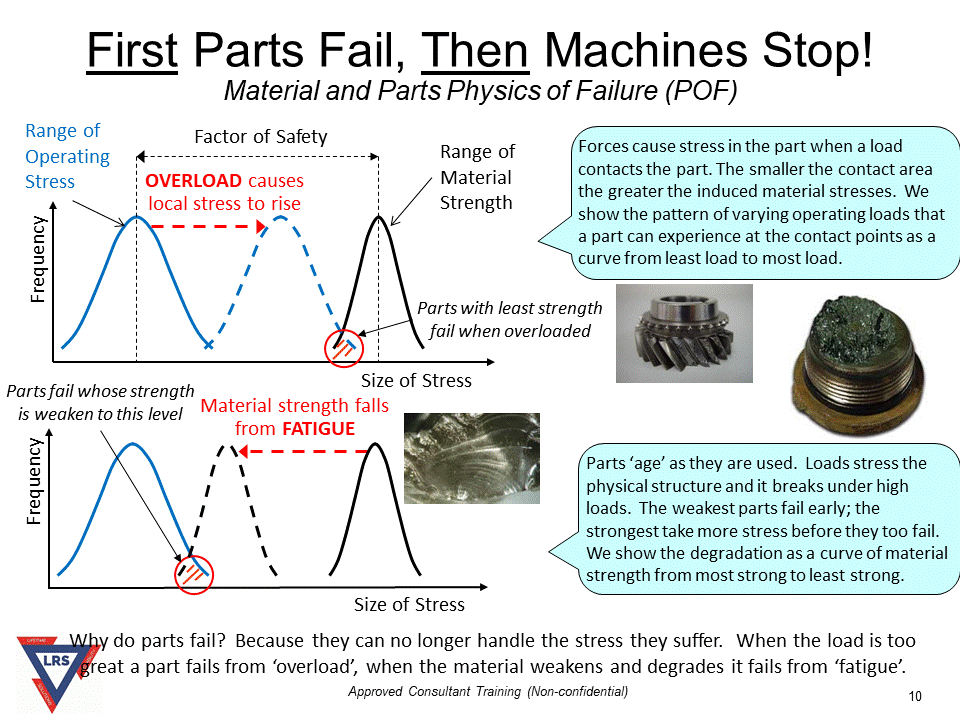
This slide applies Physics-of-Failure microstructure science to explain why parts fail and machines breakdown. The cause of parts failure can be reduced to two categories. The first is overload of the microstructure, where the material-of-construction is pulled apart. The second category is when the material-of-construction degrades, where the microstructure is removed, like in corrosion or chemical attack, or material is fatigued and separates to the point that the remaining structure cannot take the load.
When engineers design a machinery part, they start by determining the operating loads the part will suffer during its service life. The loads can vary from virtually zero when the machine the part is in is not working, through to high stress conditions when the machine is operating under severe running situations or starting up under a large load. Using this information, the engineer selects a material-of-construction to make the part. The curves shown in the top section of the slide represent that scenario.
The blue distribution curve on the left is the range of operating stresses the part will see during its service life. The left-hand y-axis represents the frequency that those stresses are seen by the part during its lifetime. The black distribution curve on the right represent the range of stress carrying capacity of the material for the part. The variability in material strength depends on the raw materials, the manufacturing process, and the quality control and quality assurance used in making the material-of-construction.
You can see that there is a wide distance between the range of service loads and the material’s load-carrying capacity. This separation between the service load and material strength is called the factor-of-safety. In theory the part will never fail because even the highest operating load is well below the material’s capacity to carry that load. Yet, if you look at the pinion gear in the picture several teeth are broken off the gear. What was meant to happen in theory during the part’s service life did not occur when it was used.
For a gear tooth to break, its material must have seen a massive overload. The service load curve must have moved to the right and the stresses on the part were beyond its ability to take. One way that can happen to gear teeth is if a wear particle of a few microns size gets trapped between the teeth of the driven gear and the driving gear. All the forces are now directed through the few-microns sized particle and onto each tooth’s material-of-construction. Instead of being distributed over the whole area of each tooth, the load is now on a very small surface area of a tooth. The stress in that small area is huge, so massive that it causes the material microstructure to fail and makes the tooth shear off.
The bottom set of curves represent the second scenario, where the material of construction is damaged to the point where what material remains cannot take the load it carries. In such situations the load carrying capacity of the material shifts to the left. As the microstructure available to carry the load reduces in size, the point eventually arrives where even a normal load is too much for the remaining material and the part fails.
There is a science to the failure of materials called Physics-of-Failure microstructure science. It covers the range of events and causes that can lead to the collapse of the materials-of-construction which make up the microstructure of the parts in the equipment and machines we use. Understanding the behaviour of materials through Physics-of-Failure microstructure science, and using the information and insights gained from it, are foundational to selecting truly effective equipment reliability creating strategy in the Plant Wellness Way EAM methodology.
Leave a Reply