
It’s easy to lose your way in maintenance, reliability and enterprise asset management. Without a vision you are aimless. Without a map you are lost. To get maintenance, reliability and enterprise asset management success you must have both the right vision and the correct path to it.
Keywords: asset management strategy, strategic asset management
To get maintenance, reliability and enterprise asset management success you need to be capable to deliver it, and you also need to do the right things that get you there. Your maintenance, reliability and enterprise asset management processes are your path to success. You must build them so you surely get the maintenance, reliability and enterprise asset management performance you want.
Figure 1 contains a message of the power that comes when people share the same vision. A shared vision brings a common focus and causes alignment of effort that allows greater things to be done.
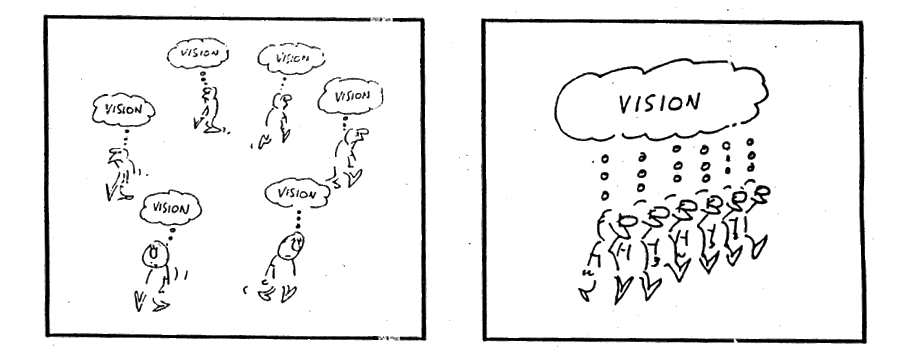
Something is missing in Figure 1 that is as critical to success as having a vision—there is no road map to success, there is no true and sure path to follow. What is the right way to get to the vision? Figure 2 shows you a third frame with the missing factor for success—the path to take to get there!
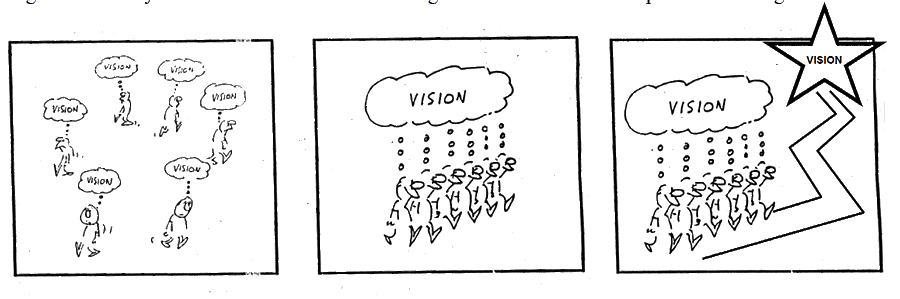
Every organization has goals. The most successful ones have a detailed plan of the pathway to get to their vision.
Some years ago research was done into what people do when we cannot see where we are going. A blindfolded man was put in the middle of a large, empty field and told to walk in a straight line. He walked in what he thought was a straight line. At the end of the experiment he was shown a film of what he actually did. He had walked in a clockwise circle. Everyone who did the experiment and lost their vision went in circles. Immediately their vision was returned they all went straight.
A company, a department, a person without a vision has no target from which to derive their direction. A company, a department or a person that has no vision ends up going in circles. For maintenance, reliability and enterprise asset management to be effective, i.e. what you do moves you towards your goals, your people need the right target in their sights.
If your target is over the horizon and you cannot see it, then your mind by itself cannot derive the right direction. You will guess a path to take. When that road comes to an end you will guess another path to follow. Your direction has some sense to it but the path will be confusing and can never be replicated again. It will take a long time before the goal is reached. If you can’t directly see your target, you will be most successful if you first have a map of the roads to take to the goal. This means you must first do research to identify the best path to use before you start the journey.
When you do detailed maintenance planning you research the path to get equipment properly maintained. The more the tasks in your work plan are completely specified and quality assured, the greater success your plan will have in making equipment more reliable. When you do maintenance strategizing you research a true path to do the most effective maintenance work. The more exact and correct the strategy is for creating plant and equipment reliability, the more uptime you will get. When you develop strategic asset management plans for operating sites you research the most successful ways to get maximum life cycle profits. If your asset plans have the ideal ways to use and care for assets at the least costs you will maximize your operating profits. Each of these undertakings starts with a vision, but to reach the right results you also need a path to that success.
What wastes and high costs must happen during a maintenance job that is not planned to the detail needed to do every task effectively and efficiently? What useless maintenance plans must arise in companies that have no clear, organized maintenance strategy to create reliable plant and machinery? How many fortunes in operating profits will be lost in industrial companies that do not know how to run and maintain their plant and equipment for the least operating cost? People in these companies have the right vision—they want effective, efficient, low cost operation and maintenance—but they don’t know how to get to the vision. The people in such companies are busy, but without a sure path to success the organization is lost and its people go in circles.
Set performance targets. Then research the details of what to do to most quickly reach each target. Follow the path that you build from your analysis. That is the simplest, quickest recipe to success. If you want world class maintenance, reliability and enterprise asset management results start by setting world class performance targets. Then find out how to do that level of performance and what must be changed in your organization to become that good. You now have your path to world class success. Having a vision of where you want to go is good. Having the map to get there is best.
We invented the Plant Wellness Way methodology to let companies design, map and build a direct route to their greatest operational success. When you use the Plant Wellness Way you plan and create a route to get to sure success. The path you build is sound, clear, direct and replicable so everyone that follows after you will reach the right destination every time. Ask a Plant and Equipment Wellness Consultant how you map and follow the Plant Wellness Way to your operational excellence vision.
Mike Sondalini
Director
Leave a Reply