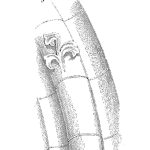
How to use Condition Monitoring Reports to do Maintenance Planning of the Maintenance Work Activities that will prevent Equipment Failure
This article by Peter Brown, a vibration analysis condition monitoring expert, explains how to address and action condition monitoring reports from your condition monitoring service provider.
Abstract
Maintenance Planning From Condition Monitoring Reports. Having developed the finest condition monitoring programme that provides all the data required to predict plant behaviour it is now necessary to convert that data into information and to plan it in for action by the maintenance team at a time that is compatible with operations.
Keywords: opportunity maintenance, condition based maintenance
NOTE: You can now do our online 10 module Maintenance Planning and Scheduling training course with certificate. Read more at Online Maintenance Planning and Scheduling Training Course.
1. Introduction
Planning maintenance work based on condition monitoring reports is essentially the role of the Maintenance Planner, and if it is not done well there will be lying around potentially useful data that has not been applied—there will be the catastrophes that follow from the lack of action.
Over the past several years in the course of auditing condition monitoring programmes and maintenance systems the writer has found that the failure to effectively handle the reports and the data/information therein is the most prevalent cause of programme failure.
To achieve effectiveness it is important for the Maintenance Planner to have:
- a good understanding of asset maintenance management,
- good communication with all concerned,
- effective work procedures and job instructions,
- ensured necessary action takes place.
2. The Condition Monitoring Report
The nature of the report from the condition monitoring technician is important. It should be in plain language and aim at guiding the tradesperson in their investigation and corrective work. If, for example, the report calls for correction of alignment and no misalignment is found it is likely the tradesperson will look no further. The problem may in fact be a weak or distorted base.
Sometimes, analysis is not certain and reports can be vague. Such vagueness should be avoided, as it helps no one in determining the appropriate remedial action. In such a situation, however, if it cannot be avoided it will be appropriate to advise operations and/or maintenance that there is an uncertain problem and a closer watch should be kept on the item of equipment in case of unexpected developments.
It should be recognised by the Planner that the uncertainty might be indicating a need for a second opinion or more comprehensive diagnosis from a more experienced practitioner. For the sake of the credibility of the CM programme it is important to deal with these issues.
It is possible that the report is kept simple but the Work Procedures provide for the wider approach to the problem at hand. If this approach is to be taken, and it is a very valid one, then there will need to be a suitable set of quality work procedures and instructions – normally a task that falls to the planner.
Importantly, however, it is at this reporting stage that data is transformed to information and is made available to all who should be aware of it.
3. Raising Work Orders
In a number of organisations the report is presented in electronic form as Work Orders within the CMMS. The report comprises a Report Summary sheet listing all the machines in a particular route or area. Against each machine a box is ticked indicating condition as Satisfactory or Unsatisfactory or Not Tested. A comments column would have a Work Order No. entered where there was an unsatisfactory condition and action was required. Concerned persons reviewing the Summary Sheet could then refer to the Work Order in CMMS for more details. The person responsible would then make their decision for action on the Work Order, to accept it with a suitable date, reject or defer to a more suitable date.
The Work Order would show that it was CM initiated and also be coded for the nature of the problem. This would greatly facilitate analysis of CM generated work.
Work priorities obviously must be a part of this process and should be assigned by the person responsible to give guidance to the Maintenance Planner.
4. Scheduling of Tests
The Planner must have the condition monitoring test schedules entered in the Planned Maintenance system within the CMMS to ensure that the tests are carried out and the reports are received.
This is particularly important with more critical plant.
It may be that some tests, such as vibration, are carried out in-house while others, such as oil testing, are carried out by contract. It will be the responsibility of the Planner, in conjunction with the condition monitoring technician to bring these reports together and identify any necessary action.
5. Opportunity Maintenance
Condition monitoring will identify equipment that has a developing fault that may not yet justify remedial action. It is appropriate to report this and to tag the equipment so that should its associated system be down for maintenance or breakdown repairs the opportunity can be taken to carry out the remedial work then rather than 2 or 4 months later – possibly necessitating a special shutdown.
6. Evaluation of Effectiveness.
CMMS systems can be used to provide information on the effectiveness of condition monitoring systems and advantage should be taken of this. At the end of the day the language of effectiveness is Dollars. Put a value on CM “catches”, extract the information from the CMMS and raise a monthly report on the savings – contribution being made to Profits – by Condition Monitoring.
This “flag flying” is important in that it:
- promotes the effectiveness of CM
- encourages other involved persons to give higher regard to recommendations
- can be helpful in supporting future requests for funding to upgrade the system and obtain training.
Significant one-off jobs involving the application of CM techniques should also be written up. This will help lift the professional standards of the CM team.
The use of measures such as Maintenance $ per Kg Product (see Session 2) can be helpful in assessing improvements made against effort/resources/changes made to a machine, or specialised training given such as an Alignment or an Awareness course.
7. Tracking of Inter-changeable Machines
The open architecture of modern CMMS and CM software readily permits the historical condition monitoring data to stay with the machine or component to which it belongs rather than with the machine location. This is most applicable to items such as motors and gearboxes which may be carried in stores as spares.
8. Feedback Information
For a Condition Monitoring Programme to maintain its effectiveness it is essential it be current with regard to the changes in machinery within the plant and also the correlation of what is actually found when a machine is stripped as opposed to what was diagnosed.
Not only is it extremely frustrating for the condition monitoring technician to find these changes have occurred whilst in the course of testing, it can lead to corruption of the historical data and reduce its effectiveness.
This flow of information will include:
- information on condition of a machine as found compared to that diagnosed
- opportunities to inspect opened machinery to gain a better understanding or obtain specific data such as numbers of gear teeth
- changes in bearing types or manufacturer
- motors or other machine components replaced by inter-changeable spares or new items
- changes in machine speeds by pulley replacement
- changes in the duty cycle or process conditions of a machine or system
- machine or system modifications
- repairs made which are initiated by other than CM
- advise of deferment of recommended work
I hope that the above helps you.
Best regards,
Peter Brown
Vibration Analysis Specialist
Lifetime Reliability Solutions
Leave a Reply