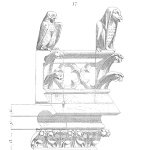
There is only one reason companies do maintenance on their physical assets—because it’s cheaper than not doing it. Unless doing maintenance makes a profit by saving money, it is wasting money. In the end, maintenance is about getting the best economics from physical assets.
Keywords: plant maintenance management, equipment reliability, production risk management
You only undertake a maintenance program for an equipment item if doing so makes more life-cycle profit for the business than the other options you could have taken. If maintenance on equipment cost your company more than letting an item fail and replacing it with a new item, you would not do maintenance because the operation would lose money.
You eventually replace equipment when the total cost of its continued use makes less profit over the same period than buying, installing, and using a more modern replacement. You buy new or replacement equipment because it makes more operating profit than maintaining and using the existing asset.
Maintenance is an Economics Decision
Doing maintenance is based on whether it is the most economic business choice. You don’t maintain equipment because it needs care and repair; you do maintenance because it makes more money than doing any of the other equipment use and upkeep choices you could have made. Any company that does not annually do life-cycle financial modelling of their equipment maintenance options versus their replacement options versus their hire and lease options, and so on, does not know how to maximize its profits and is surely doing too much unnecessary maintenance and paying far too much in maintenance costs.
This means that at any time in the life of an operation, the future maintenance effort undertaken must make more profit than doing other alternatives. To make the highest profit for the company, it also means that your maintenance group and outsourced maintenance service providers need to be stopping, reducing, and solving the problems that cause maintenance.
Maintenance makes a profit contribution every time it reduces the failure rate of maintained equipment. The best long-term justification for doing maintenance is to achieve the results shown in Figure 1: reduce the number and frequency of failing parts so that you get more uptime at lower maintenance expense, to make more production at ever-decreasing costs with ever-greater profit.
If you only use maintenance for care and upkeep of your machines, without making the machinery more reliable, your maintenance efforts are not generating the most profit for your operation. It also means your plant and equipment are degrading faster and requiring replacement sooner than would be the case if a component reliability growth program were in use.
Figure 1 also lists all the responsibilities that your maintenance group and subcontract service providers should be delivering for your company. The maintenance people should be positively contributing to every one of the bulleted items, either by doing it themselves or by feeding back to the appropriate parties what they know and have learned so it is done more profitably in future.
To justify its existence in a modern company, maintenance must become a profit centre and generate income. Maintenance is not done to care for and maintain equipment; maintenance is done to maximize profit because it generates more money than doing anything else.
Reliability, Safety, Operating Risk and Maintenance are Interconnected
The correlation between safety and reliability is striking. Safety data from industrial sites show a clear inverse relationship between equipment reliability and injuries—plants with exceptionally reliable equipment have far fewer injuries.1 The logical connection between higher reliability and fewer safety incidents is easy to explain: the greater your plant uptime, the fewer repairs you have to do, and that means fewer opportunities for injury to operators and maintainers. Reliable machines and equipment are safer machines and equipment.
With perfect equipment reliability, there are no failures and no risks arising from equipment failure events. This clear relationship between risk, safety, and reliability gives you two highly beneficial risk reduction strategies that are guaranteed to deliver a safer workplace.
1. Lift your equipment reliability so that fewer breakdowns happen: this removes opportunities for injury during repair while delivering more plant uptime and lower maintenance costs.
2. Intentionally keep your equipment healthy and in good condition so that you prevent failures: this creates a safer workplace and also gets you more throughput of on-quality production.
Whenever the chance of a plant and equipment failure is reduced, your organization is guaranteed to get improved safety results because you create a lower-risk operation. By intentionally making your equipment more reliable, your workforce benefits from having fewer known and unknown workplace risks, and the company profits from a safer and more productive plant.
You’ll get noticeably better workplace safety performance when you identify the hazards inside your operating assets and proactively put in place effective life cycle asset management, production and maintenance strategies and tasks that control them.
All the very best to you,
Mike Sondalini
1 Ron Moore, RM Group, Inc., “Correlation of Injuries with PM & PdM Maintenance Work Orders and with Corrective & Reactive Work Orders” (presentation, Knoxville, TN, 2007).
Leave a Reply