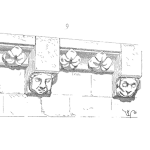
Prevent centrifugal pump failure modes starting by removing their failure causes and make your pumps highly reliable.
There are over 600 failure causes that will make a centrifugal pump set fail. How many of them apply to your operation?
A rather interesting insight happens when you first look at this spreadsheet listing over 600 failure modes in a centrifugal pump set—there are so, so many of them. Luckily you have a second, hugely more profound insight once you realise what you are up against.
The lists in the spreadsheet were put together by researching the Web for centrifugal pump failure causes, including failure modes of components in the wet-end, the bearing housing, the drive coupling, the electric drive motor and the base with foundations. I took all the failure causes for each failure mode off the Internet by doing a web browser search of articles and websites describing centrifugal pump failure, bearing failure, impeller failure, etc. It took me about two days to do the research and compile the lists into the MS Excel 97 format spreadsheet you can download.
Hopefully there are not too many failure mode duplications, nor that I have left too many centrifugal pump failure modes and failure causes off the list. I would not be surprised to learn there are some double-ups, though I was careful and there should be few duplications.
The image below shows the centrifugal pump set failures as a cause and effect tree. I could not fit 600+ causes in one slide, so the cause and effect tree categorises the failures by sub-assemblies. If someone tells you that a centrifugal pump set has failed and you have to find the root cause, you are confronted with 600+ causes to investigate. What do you do with over 600 potential failure causes to look at?
Without having the failed item as evidence, it is a crazy and pointless task to investigate a failed pump set, because it could be anyone of 600+ causes. That is why the evidence is so vital in a root cause failure analysis (RCFA); only the evidence can confirm the actual route the failure took from cause to incident. Any RCFA done without the complete evidence is at risk of going off track and fixing a thing that did not cause the failure.
Once you view the list, the first insight you get is that there are sooo… many ways to fail centrifugal pump set components. (Remember, the list was developed from articles and information off the Internet written by people describing known equipment failures and causes.) If in just one piece of common industrial equipment there are over 600 ways that it can knowingly fail, what happens if you have dozens, or hundreds, of centrifugal pumps in your operation?. With so many opportunities to go wrong—tens and tens of thousands of possibilities—you risk suffering many and regular failures of pumps. Once you consider the possibilities for failure in the assemblies and component parts of all the machinery in your whole operation you are talking about millions, and up to billions, of potential failure sites.
How do you handle that scary reality and keep your plant and equipment working reliably so that your company can stay in business profitably? (An awful lot of companies do not address that problem well. That is why Plant and Equipment Wellness Way was created. Now every company in the world can be hugely reliable for the least life cycle cost.)
But the most profound insight is the second one—all 600+ failures belong to only two broad types of failure causes. They are either caused by human error and misunderstanding, or they are caused by Materials-of-Construction failure. Human error and lack of knowledge is controlled by error proof practices like the Accuracy Controlled Enterprise 3T Standard Operating Procedures. Materials-of-Construction failures are prevented by the Precision Maintenance practices listed in the following image.
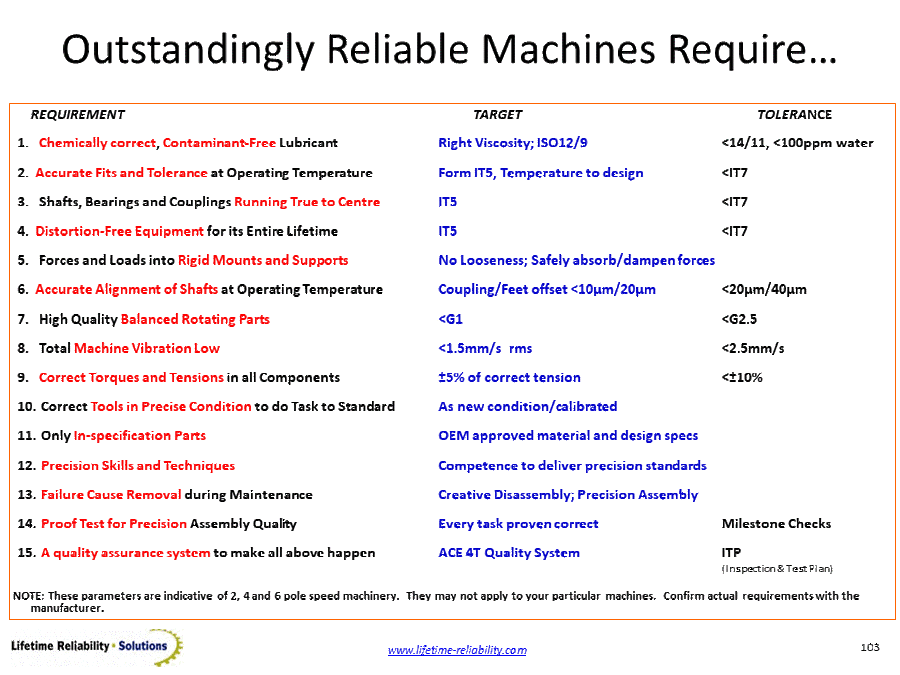
Long lasting, high reliability pumps do not have failure modes because the failure causes that produce the failure modes are prevented. For example, in high reliability organisations pump failure modes caused by misaligned pump and drive motor shafts are prevented by proactive shaft alignment done on a regular two-year frequency. High reliability organisations do not allow lubricating oil to degrade in the bearing housings; they ensure the oil is clean by removing wear particles and preventing water absorption.
In companies with highly reliable machinery and pumps they do not wait for problems, nor do they do a lot of condition monitoring looking for problems, rather they set precision maintenance standards that prevent machinery problems and they proactively ensure that the machines are kept at those standards of machinery health and wellness. Their maintenance crew removes the failure causes by regular proactive precision maintenance to put machines back into precision health condition. As a natural result of that approach to creating high reliability there are no failure causes left unchecked for so long that they start pump failure modes which can lead to pump failures.
To which you must also provide precision operation practices that address the problems listed in the image below, so that you stop your equipment operators destroying the machines, plant and equipment. Human error, operator error, maintenance error… they all result in broken machines. None of which had to happen.
A company that has many centrifugal pumps in their operation will have a lot of work forevermore if they approach pump reliability in the wrong way. Most companies I know would address pump failure modes as they arise. They would fix a pump failure after it happens or correct a pump problem after they find it with condition monitoring. That way of looking after centrifugal pumps guarantees that you will always have pump failures.
If you wait until a pump has failed, or you wait until your condition monitoring tells you a pump failure mode has started, you naturally end up fixing problems. Yet what you want is not to have the problems in the first place. You cannot have failure-free pumps and machinery if you wait until you have a failure mode before you fix the problem.
You can also look at these two articles if you need more information on how to get outstanding pump and machinery reliability: What is Equipment Reliability and How Do You Get It. The second article you should read is Setting Maintenance and Reliability Standards for High Machinery Reliability.
My best regards to you,
Mike Sondalini
Managing Director
Lifetime Reliability Solutions
Great article! Thanks for the detailed research and for sharing. I love the list of Failure Modes/Causes. Great to have it in one’s back pocket for FMEAs or RCA exercises.