
Human error causes 80% of plant and equipment failures. It is the single factor, which if controlled, makes the most difference to achieving world class equipment reliability and operational success. With the introduction of low cost communication and visual devices it is now possible to assist maintenance workers proactively prevent human error. By using interactive audio-visual devices workers can be coached through a job error-free to get right-first-time quality every time.
Keywords: work quality control, defect elimination, human error prevention, error detection
Human error happens because we are human. As flesh and bone creatures our muscles fatigue; our mind tires; we age and get weak; we lose focus when distractions take our attention. There are endless opportunities for all of us to make mistakes. Human error is inevitable and occurs regularly. But just because human beings make mistakes it does not mean failures must happen.
Maintenance interventions in plant and equipment cause Early Life Failures. Also known as Infant Mortality, repaired machinery or equipment fail soon after it is put back in service. It is a phenomenon identified by Conrad Waddington during WWII when he analysed failure history of British aircraft and found that aircraft downtime increased soon after being maintained. It was given the name the Waddington Effect. Figure 1 aims to highlight that up to 70% of failures in mechanical equipment are early life failures and 30% are induced-stress random failures. These are nearly all due to human errors that occurred at various points in the life cycle. The aim of human error control is to reduce the incidents of human induced failures.
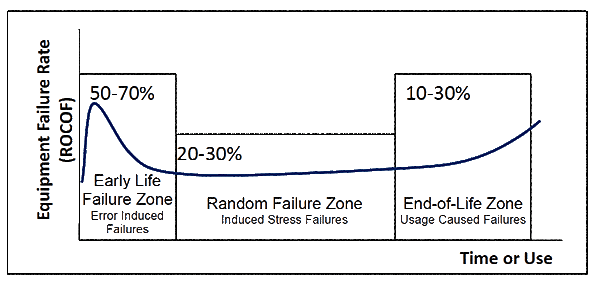
Figure 1 Rate of Occurrence of Failure (ROCOF) in Mechanical Equipment
What is Human Error?
Human error is a mistake made by a person that produces a detrimental outcome. It is a normal by-product of human activity. The limitations of humans listed in Figure 2 are the foundations of human error. We all are affected by them in various ways throughout situations in our lives. One could reasonably argue that all failures are the fault of the designer because their design allowed them to happen.
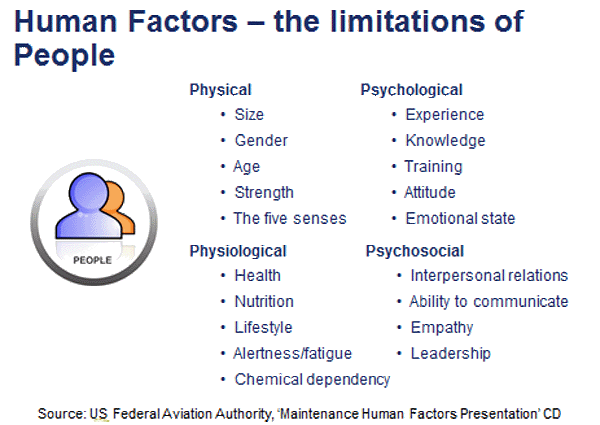
Existing Methods of Human Error Detection
One branch of human error management strategies rely on finding an error once made. They do not stop errors, but detect them after they exist. The most common methodologies used to detect human error are:
- Inspection and Checks: Samples are tested for non-conformances against a standard.
- Process Audits: Inspecting work process outputs and using information gained to control the process (a feedback loop)
- Point-of-Origin Inspection: Assess beforehand if the conditions are right for error-free outcomes. For example, Lean Manufacturing Poka Yoke uses low cost devices to spot mistakes as material moves to its next processing step.
Existing Methods of Human Error Prevention
The second type of human error management prevents error. It recognises the effect of human factors and requires designing a system-of-work to remove or reduce the opportunity to make a mistake. Standard Operating Procedures, Fatigue Management, workplace ergonomics and Safety Management are examples of systems and methods to prevent human error.
We have long understood that preventing mistakes is far cheaper than fixing them. The admonishment of ‘An Ounce of Prevention is Worth a Pound of Cure’ is ascribed to Benjamin Franklin (1706-1790). The 1-10-100 Error Cost Rule has long been known in quality management literature. Figure 3 shows the 1-10-100 Cost Rule where a mistake that progresses through each level costs ten times as much to fix than the prior level.
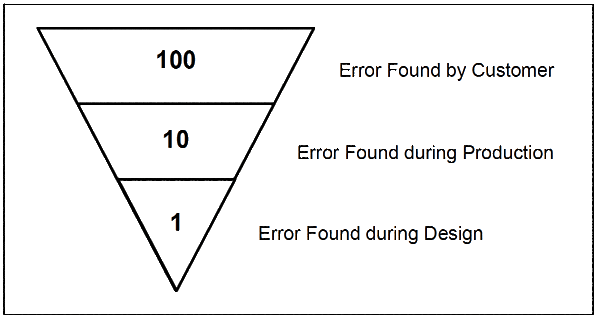
The 1-10-100 Cost Rule makes it clear that it is best to detect error early. The misunderstanding people make when they see the 1-10-100 Cost Rule is that a mistake found at data entry is not expensive to fix. So they look for errors early in an items life, but forget to count the time and cost lost looking for errors. They overlook that in an imperfect business system run by humans some errors still get through inspection to cause disaster. They mistakenly believe early error identification is the aim of quality management. Much better by far is to not make errors in the first place. Solutions that prevent error bring far greater value and productivity to companies than solutions which identify errors for correction.
Anti-Mistake and Error Prevention Solutions
To make serious reduction in human error rates we need solutions that prevent and remove the opportunity for mistakes. We need solutions that have the effect on lowering equipment failure rates as shown in Figure 4. Such successes will single-handedly stop nearly all early-life and random failures and thereby get outstanding reliability for the entire equipment lifetime.
The best anti-mistake solutions are those that are designed and built into the equipment. The machine design protects the machine from human error caused failures. The design insures that there is only one way to assemble parts and any other way is obviously wrong. You would be justified to retrofit your machines with human anti-mistake solutions if the cost of fixing one incident of human error is more than the cost of its prevention. Where the same human error happens twice it should be mandatory to installed designed-in anti-mistake solutions.
Where machines allow human error, and the machine design cannot be changed to stop mistakes, we are left with the option of helping people to do fault-free work. Trouble-free work is the purpose of written work instructions (WI) and standard operating procedures (SOP). These documents count on people exactly following a known method of achieving success. But they do not stop mistakes. Fortunately, modern technology lets us make SOPs and WIs interactive.
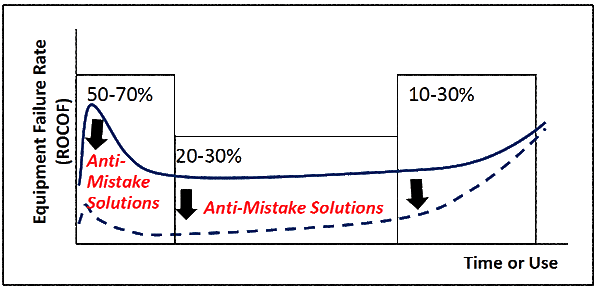
Interactive Information Systems for Maintenance Work Error Prevention
As technology progresses new opportunities arise to deliver low-cost, simple techniques to prevent human error. Now that text-reading software is near perfect, voice recognition software is highly accurate, on-board digital cameras are small and cheap, heads-up display visors are common, touch-pad devices are hand-held and inexpensive, and wireless communication is standard, a new opportunity arises to prevent human error in maintenance and assist maintainers to do their work tasks right.
Today’s maintenance man can be digitally connected to the information they need and conduct real time interaction with documents, drawings, component engineering details and information databases. They can collect job data and talk straight to databases, take component and job quality photos, record measurements on hand-held devices and put them into work order history.
All the necessary elements for full digital exchange between maintenance and engineering databases and a man working remotely on the job are shown in Figure 5. Job procedures and work instructions can be read electronically and spoken to the technician. Step-by-step a maintainer can be taken through each activity. They can get what information they need for themselves. They can even be connected to experts who are ready to help them with difficult situations and decisions. With the aid of technology the risk of human error is proactively reduced so that mistakes become highly unlikely.
Interactive information systems for maintainers have become a necessary standard to greatly reduce the odds of making oversights, slip-ups and inaccuracies. Before maintainers act they will know the right action to do. When they face uncertainty in their job, or incomplete engineering knowledge, they enquire in the databases and receive the needed information immediately. When activities are unacceptably risky a computer will talk them through a specifically written interactive work instruction designed to keep them safe. They will correspond with persons anywhere on the planet using on-board audio and visual communication. They will talk and film and automatically register what they do and what conditions they find in the plant and equipment they work on. Information will be sent wirelessly to databases or recorded onto electronic media they carry with them if remote wireless contact is not possible.
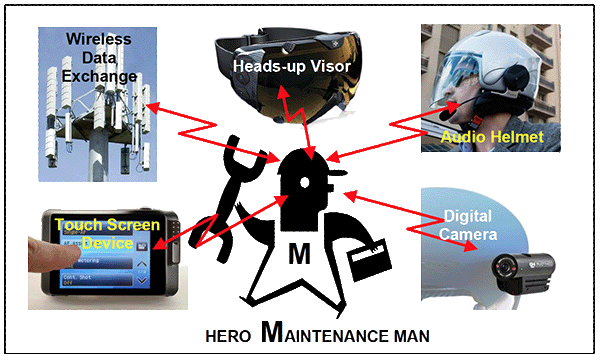
When existing written WIs and SOPs are not sufficiently informative to provide good interactive instructions they are simply rewritten to include the vital content needed by a maintainer. Details only ever available from the original equipment manufacturer or ‘secrets’ known to long experienced employees and supervisors can be added into interactive WIs and SOPs so that all the vital knowledge is made available and is communicated to everyone who needs to know it for as long as a machine is used.
Once work instructions and procures are interactive the problems caused by human error in maintenance greatly reduce. Workmanship quality will greatly improve as every technician will proactively get the right information they need to do an excellent job. Using what is now common technology you can give low-cost ‘mentoring’ to every maintenance technician and even to operators. Less experienced and knowledgably people will deliver the work quality and performance of highly experienced and competent people because the interactive technology gives them the knowledge and work practices of highly capable technicians. With complete and correct information immediately available to the man at the workface in a form they interact with and can proactively confirm what they are doing; opportunity for human error greatly reduces.
The workplace will be safer, jobs will be better managed, more tasks will be done accurately, right-first-time, and work history will be fully and properly recorded as the work is being done. The control gained over human error with interactive information systems will usher in world class reliability business wide.
My best regards to you,
Mike Sondalini
Leave a Reply