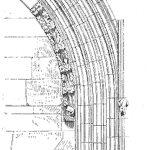
Which critical spare parts you carry in the maintenance store always revolve around how much risk your company is willing to bear. It is purely a risk based business decision. Look at the economics of the risk decisions available and go with the biggest chance of success.
—
I have a question about critical spare parts determination that I always have a problem with. I do not know if this topic is included in the online preventive maintenance training I and my team of engineers are doing with you, that’s why I am asking the question.
How can I determine which are the critical spare parts that we have to keep on stock?
I’ve already read a lot of books and articles on it, but to be honest I do not think it is very easy. It is one thing to write something into a book, and another situation when facing the reality of a machine breakdown with no parts available, or faced with a claim from senior management that we have too much cash in the warehouse tied up in parts.
When my engineers ask me about it, I feel that they have the same difficulty to determine the spares because each part can breakdown. It seems to default to two main options for them.
- They want to order almost another machine to keep on stock, but of course this is not the right solution.
- They order almost nothing.
Do you have any method for this decision? Thank you in advance for your clarification and help.
Hello Thomas,
Critical spare parts are the parts within critical equipment that, should they fail, will badly reduce or stop production, or harm our business, or a person, or our community, or our world. I call such components the ‘working parts’. It includes everything used within an asset’s chain-of-part needed to make an item of plant work correctly—electrically, electronically, mechanically, structurally, and software. The asset chain-of-part is all the equipment components needed to make an asset operate as designed. The power cables from the power provider are in an asset’s chain-of-parts. The switch board distributing power is in the asset chain. The oil in a machine’s gearbox is part of the asset chain. The hold-down bolts in a machine’s feet are part of its asset chain-of-parts. The PLC program controlling an item’s operation is in the asset chain.
LET US REVIEW THE LOGIC OF WHY WE BUY AND CARRY CRITICAL SPARE PARTS IN OUR MAINTENANCE PARTS STORE
Presume you do not buy any spares at all for any of your plant and equipment. You start into production with no spare parts of any sort, not even a nut and bolt, or a drop of top-up oil. If you drive a car you do this every time you use it. There are few drivers on the planet who carry their own spare parts for their car. I’ve driven cars for decades and never carried a spare for any of them. There was no need to. My strategy is to buy reliable cars new from reputable manufacturers. The car will never stop from parts failure during the next 7-8 years of use provided I do the preventive maintenance (PvM) on a critical component before there is a risk of its failure. I’ve only ever been stranded in a car that won’t go when its battery died. That won’t happen again if I include a battery replacement of old-with-new in every three year PvM service (or a longer replacement period if the battery is sure to last that long).
The justification for keeping your own spares is not only loss of production, more correctly it is the total business losses caused by the part’s failure. If I could find an insurance company to carry all my business risk and pay my business an equivalent replacement income after a production plant failure, I then do not need to carry any spare parts. Once any equipment fails my Insurer will pay me the same income as I had when the plant was working—we’re still making money, but not from our production plant, it’s now coming from our Insurer’s bank account. Such insurance does exist, it is called Business Interruption Insurance. In such a situation I will not keep spares, but will only buy them when they are needed, which is after the failure. This is another strategy where you cannot justify storing parts because the Insurer will carry all our costs of failure at no loss to us beyond paying the Insurer’s premium. In the real world your Insurer will tell you to carry insurance spares. Your Insurer is run to maximize its own profits and it will force your company to reduce the risk of losses it must cover.
You only carry a spare part in your company when there is unacceptable risk to your business should the part fail. If the part will never fail during its operating life in your company there is no need to also have a spare—it would be a complete waste of money. The only time you can justify carrying spare parts is if your Insurer will not carry the risk of failure, or your company cannot afford to carry the risk of failure themselves. Your task when you want to justify critical spare parts, is to prove the risk from a critical part’s failure is too high by any other strategy when compared to having critical spare parts in your own store. The only reason for having a ready-to-use spare part yourself is it is the most beneficial short term and long term business loss minimization strategy to use.
DETERMINING WHETHER OR NOT TO CARRY CRITICAL SPARE PARTS USING A RISK MANAGEMENT APPROACH
You learnt in the Preventive Maintenance training course how to determine equipment criticality. You learnt how to estimate DAFT Costs from a failure. You have used a risk matrix to grade Equipment Criticality. This approach can now be applied to determine the risk your Company carries should any of the working parts in a critical item of plant fail.
You can now understand why it is a highly successful physical asset management strategy to have plant and equipment made of the same parts. Since the parts are common you can share the spares. This means fewer spares are needed in a smaller maintenance store. That will make your senior management very happy. But this strategy can only work if senior management mandate its use in the first place. It is amazing how much of a company’s success depends on senior managers understanding where the costs come from in their operation and then making simple, smart rules to optimize them!
One key recommendation to help convince senior managers is to show them the risks of the various options visually on your company’s risk matrix. Let your management see the risk they carry by not having their own critical spare parts in store. You know how to estimate the DAFT Cost of failure for each part. The likelihood of failure for each working part you can estimate from historical records. Thus you can plot the estimated business risk of not carrying the part yourselves. Next you estimate the DAFT Cost if you did carry the part in your own store. When there is clear financial benefit in carrying a part in-house you have justified its purchase and storage awaiting the next failure. When there is a large risk reduction by carrying your own critical spare parts you can be sure it is the best business loss minimization strategy to adopt compared to other viable choices available to you.
To stop the risk of unexpected breakdowns each working part’s reliability must be 100% for all its operating life, or else you need to remove every opportunity for its failure during it service life. Otherwise you must carry critical spare parts in your maintenance store.
For all critical spare parts, go with the strategy that brings the highest probable business loss reduction for your company. No one can know the future, but by basing your decision on the results from the risk matrix you have arrived at the best chance your company can take to carry the right spares to minimize its operating risks.
Let me know if you have more questions about the above.
All the best to you,
Mike Sondalini
Leave a Reply