
Design-out maintenance is a root cause failure elimination category where the solution is to design for reliability and intentionally create highly reliable equipment through an engineering design change.
—
I am a design engineer and am considering plant improvement as a more proactive activity for our department. Being in design I am interested in design-out maintenance solutions and the role they play in maintenance cost reduction. Particularly where design out solutions are used for failure elimination.
I like the words of Michael V. Brown, “Many right minded industrial organizations have adopted the seemingly unattainable goal of ‘All accidents are preventable.’ They know that the goal helps people focus on the ways to prevent accidents, i.e. reducing unsafe conditions and unsafe acts. A similar approach should be taken with respect to equipment failures in a plant. Focusing on a goal such as ‘all failures are preventable’, or ‘all downtime is preventable’, leads plant personnel to identify the causes of failures and discover ways to reduce them.”
I am doing some research in the field of design-out and wonder if you have case studies or methodology regarding design out.
Hello John,
The definition of Design-out Maintenance from the Asset Management Body of Knowledge (AMBoK) is: The Maintenance tactic whereby changes or modifications are done to the equipment to remove a failure cause, or to allow other maintenance strategies to be applicable in managing the consequence of the failure.
This definition is a dichotomy: Design-out Maintenance cannot mean both re-engineering to remove the cause of failure, and at the same time allow failure in a better-managed, less-costly fashion.
To manage the consequences of failure and ‘allow failure in a better-managed, less-costly fashion’ is merely a change in maintenance strategy and/or operating strategy to those actions that deliver lower maintenance costs. In other words, you change your maintenance and/or operating practices and methods to reduce stress in your equipment components. Any time you reduce stress in machinery and equipment parts you will increase the time to a component’s failure. You have not actually designed-out the causes of failure.
You could make an acceptable argument to satisfy the AMBoK definition if you said that by changing maintenance and operating strategy you ‘design-out’ failure causing problems from your maintenance and/or operating processes. But for me ‘design-out maintenance’ is taken for its literal meaning: the elimination of maintenance through the creation of reliability by design.
In that case, the definition of Design-out Maintenance is: The eradication of a cause of failure from a component by a reliability creating engineering design change. Design-out is used to engineer high reliability parts into machines, plant and equipment because the risks associated with the failure are too expensive to accept.
In Reliability Centered Maintenance (RCM), design-out is a necessary final solution when maintenance and/or operating strategy is ineffective in sufficiently reducing risk. In RCM, design-out is where parts are re-engineered to prevent a failure mode(s). This is evidence that ‘design-out’ really means reliability improvement by an engineering design change, and does not include in its meaning a change in maintenance or operating strategy (which are actually business process changes).
DESIGN-OUT MAINTENANCE AND DESIGN FOR RELIABILITY
Proactive reliability-creating, design-out solutions include the likes of: Failure Mode Effects Analysis FMEA, Physics of Failure Analysis PoFA, Highly Accelerated Life Testing HALT, Highly Accelerated Stress Screening HASS, and more. In these design-out methodologies you remove opportunities for failure through component design changes. In a new design you prototype it and intentionally make it fail, while looking for failure modes to design-out. In an existing design you re-engineer it so that there are fewer failure modes when in service.
Finite Element Analysis FEA is a useful computer modelling tool to ‘virtually prototype’ component designs. Before making the part you model it digitally and apply computer-generated stresses to it. The stresses simulate what might happen in service and you can see the component’s weaknesses as it distorts and distresses from the virtual loads and forces. But you should also make a real component and put it in a real machine and stress it through failure testing trials to identify failure modes.
DESIGN-OUT MAINTENANCE AND RISK REDUCTION
There must be economic value from having a better design. You would only make changes to a design because it is less costly than not doing so. This immediately implies that operating risk drives the need for a design change. In the figure below you can see when design-out maintenance becomes viable—if the consequence of a single event is unacceptable, and also when you have many repetitive failures.
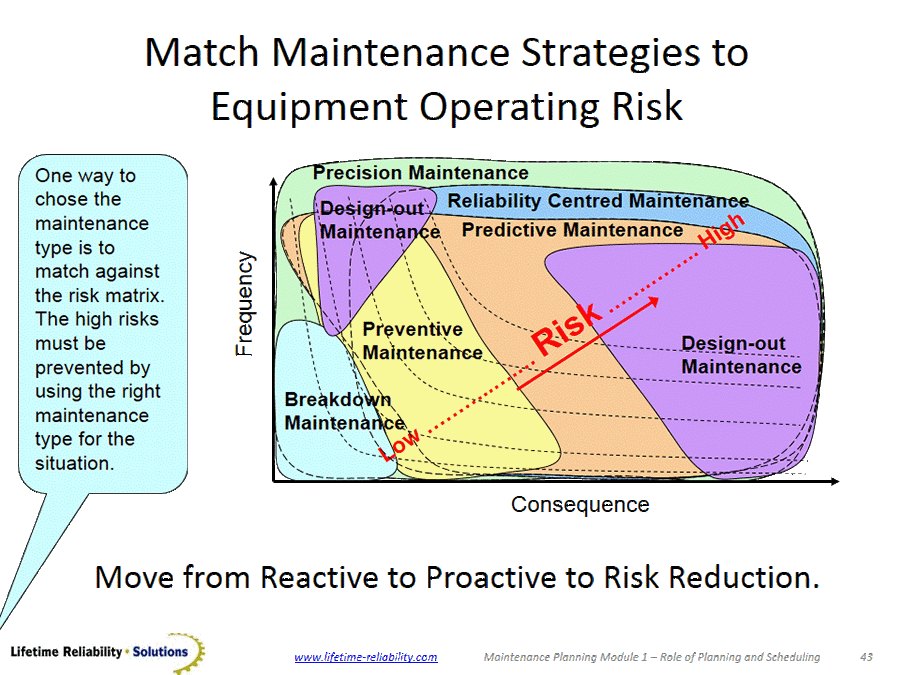
With design-out reliability improvement you make better engineered designs. You create high reliability components that do not fail as often. You eliminate failure causes so parts do not fail from current failure modes. Design-out gives you a powerful methodology for defect removal and failure cause elimination so maintenance is not required.
My best regards to you,
Mike Sondalini
Mike, I think the definition suggests two essential assumptions.
1. potential risks are known
2. identified root causes are validated
For machines, which primarily subject to wear out failures, those assumptions might not be an issue, but not likely for electrical and electronic equipment.