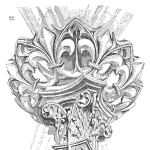
Let’s say that you and your team have done well. Your products or systems are reliable. They work, customers are happy, and the cost of unreliability is low. That’s the goal, right? Congratulations are in order.
However, enjoying great reliability performance was the goal. It is what we expected. It’s what we worked to achieve. Now what?
Past Performance and Margins
After achieving consistently reliable products, it’s easy to ‘dust off your hands’, stand up, and look around for another challenge. The team’s ability to design and produce reliable products is integrated into the process. It’s what we do.
Other important business objectives will command attention and resources. Improving product margins, streamlining supply chains, reducing development costs, etc., will vie for a piece of what was devoted to reliability-related activities.
Symptoms of this shift happening include:
- Less or no reliability-related training
- Fewer mentions of reliability-related topics, risks, or metrics
- Reduction or outsourcing of reliability-related resources
It happens because an organization can only focus on one or, at best, a small number of priorities. At some point, your organization decided to focus on improving product reliability performance, and it did. Now, it’s time to focus on something else. This shift in focus often leads to the degradation of reliability performance.
Environmental and Use Changes
A critical element to creating products or systems that meet your customer’s reliability expectations is understanding where and how your customers use your product. This takes effort. It also takes effort to maintain accurate environmental and use conditions.
Unfortunately, with great field reliability performance, it is possible a team will believe they fully understand their customer and stop or reduce work to maintain and adjust that understanding. One thing is certain: customers change where and how they use a product.
A product’s reliability success engenders customers (and marketing teams) to expect the product to work in different conditions or ways, often pushing the boundaries of what the product can withstand or accomplish. If the design and production do not adjust to the new conditions, the chances of product failure increase.
Success and Less Scrutiny
The basic problem is that once successful, we (individuals, teams, and companies) tend to lower the focus and resources on the practices that led to success. This is natural and logical. Changing how we design a product is more difficult than maintaining a process once it’s working.
The issue is we tend to pull back too much.
Steps to Avoid These Traps
The first step is to recognize that the team that created the reliability success will change over time. We, as an individual, team, or organization, will forget. Henry Petroski wrote about this issue in the book Design Paradigms. He talked about how a team’s set of decisions and considerations evolves. Initially, we were conservative, which tends to lead to designs with more margin, thus robust to a broader set of stresses. As the team changes due to promotions, departures, and new hires, the initial set of factors guiding decisions erodes. Designs become less robust. Over time, the team creates a product that is not robust enough for the stresses it will experience.
By recognizing this may occur, a good practice is to codify the reliability-related process, design guidelines, and decision considerations necessary to create a reliable product. Update product life cycle documents, business policies, and best practices in an effort not to lose the knowledge gained.
Another step is to highlight the value provided to the team, organization, and customers by having reliable products. This is difficult, as the erosion of reliability performance will be slow and, at first, very minor. Yet, keeping track permits comparisons and detection of significant changes over time. Done well, this includes not only metrics but the value calculations to illustrate the impact a lack of focus on reliability is causing.
Finally, celebrate every step toward improving reliability and identifying deficiencies. Help tell the story that reliability is important and valuable based on the successes or failures. The intent is to support the culture that we do the activities that create reliable products.
Hi Fred,
great article. I would like to add one point: documentation. How many development reports are written nowadays in the companies? While Powerpoint presentations might be incomplete, a report must contain all the details needed to comprehend why a design is like it is.
In my opinion well-written reports belong to a good engineering culture!
Thanks for the note, Enrico, and yes, documentation is an essential element of a high-performing development culture. I also agree that it is rarely done well. cheers, Fred
Thanks for the reminder that reliability work isn’t done when the product ships. A major part of quality is process control. Why not Statistical Reliability Control? https://fred-schenkelberg-project.prev01.rmkr.net/statistical-reliability-control/#more-522710