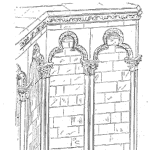
Selecting a supplier for components or subsystems involves many aspects including the desired reliability performance.
Once selected the ability of the supplier to provide items that meet or exceed the reliability requirements relies on their understanding of the requirements and operational conditions related to the specific item within the system. It also relies on the supplier’s knowledge of their own design and manufacturing processes as it related to the reliability performance.
Specifying reliability tasks, such as FMEA, HALT, ALT, demonstration testing, etc.
Does little to actually guarantee the item actually meeting requirements, unless the implementation of the activities is of value to the supplier. The specific activities described in other parts of this section outline how to evaluate the effective application of the activity. One way to assist suppliers is to not make specific activities requirements. The objective is to receive items that meet requirements for the end users, not to practice the use of various reliability-related tasks.
Instead ask the supplier to provide the accumulated evidence, at specific points in the program, detailing the current estimates related to the reliability requirements. The evidence presented is at the discretion of the supplier and evaluated by the program for suitability. Does the evidence come to the natural conclusions presented?
They should provide a logical, coherent argument.
Item failures occur due to a wide range of design, supply chain, and manufacturing related causes. The design may select a material that rapidly deforms, the supply chain may provide a batch of faulty components, or the manufacturing process may have insufficient capability to meet the design specifications. The supplier faces all the challenges the development program does from concept through use.
Therefore the reliability case should address the identification of risks, reliability estimates including methods and assumptions, plus information on the supply chain and manufacturing monitoring and state of process stability and capability.
Approach
The use of many of the reliability activities discussed in the current textbooks may apply.
The evaluation of the case involves understanding first if the evidence provided support the stated claims related to performance. Second, involves evaluation of the assumptions, implementations, and use of the activities to make design and process decisions.
The evaluation of a reliability case is not a checklist of the presence of specific tasks or activities.
Is it a good case?
Each item provided by a supplier will have different available information, constraints, and capabilities. The RAM case provides a view of how the supplier approaches creating an item that meets the RAM requirements.
There is no one right answer or set of content. Rather, given the resources available does the evidence support that the supplier fully understands the risks and sources of item failure well enough to project reliability performance in the intended use.
As an example, a case based on industry standard tests when each test relates to the dominant or expected failure mechanisms with appropriate acceleration models may provide sufficient evidence to support RAM claims. Whereas, if only relying on meeting select industry standard requirements without comprehension of converting the testing results to use conditions or reliability estimates, shows little support for claims.
Another supplier may provide experimentally verified physics of failure models, along with a long track record of capable and stable manufacturing processes. The details of the reliability case depend on the complexity, technology, and history or familiarity with reliability aspects of their product.
Value to you
Requesting and obtaining confirmation that specific reliability activities occur does not result in the supplied item meeting reliability requirements.
It only means the supplier accomplished the task which may or may not have any impact on the item’s performance. The intent of using a reliability case is to ask the supplier to support in a logical way the claims they make. The value is improved performance.
There is no one way to achieve requirements, thus working to understand the approach taken by the supplier, not the one imposed, will reveal the supplier’s strengths and weaknesses related to reliability performance.
It is also possible for the program to learn about of advanced model and reliability activities that may be useful for other parts of the program.
Related:
Are Your Suppliers Really Committed to Reliability? (article)
Leave a Reply