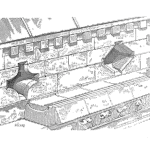
A common question concerns the warranty period.
How long should we, the manufacture guarantee that our product will work as expected? Do we include limitations or not? How do we decide?
The warranty policy includes setting the terms and when and how to extend warranty protection beyond the contracted terms.
Replacing a product for a customer may keep a customer, as opposed to losing the customer to the competition.
Setting the Warranty Period – Customer Expectations
There is no hard and fast set of rules to setting a warranty period.
It is a balance of customer expectation, competitor warranty stance, product technical capability, and cost. Your organization may have a policy, written or not, about setting policy terms and conditions.
Customers have an idea of how long they expect to use a product. A coffee shop takes out coffee cup should function at least till you have finished the coffee. We do not expect a paper cup to hold coffee and keep it hot for the entire day or longer. For a car, consumers may expect 5 to 10 years of trouble free use. Solar panels have an expectation of 30 years of use or longer.
Beyond considering the expected use period, consumers also consider the risks involved with failure. If the expected failures are relatively minor and quickly remedied, a short, limited warranty may work well.
If the failures cause catastrophic damage or require complete replacement, consumers tend to expect a long duration and comprehensive warranty.
Competitive Landscape
The market or the warranties offered by competitors also has a role in warranty policy.
If the typical warranty is a limited 3-month warranty (common with laptop computers at one time), offering a full warranty for a year signals this product is better than the competition.
There are two reasons to have a better (better, more coverage) than your competition.
First, your product actually is notably more robust or reliable than the competitor’s products. If your product fails less often you may be able to encourage additional sales with a generous warranty and not incur significantly higher warranty costs.
Second, extending the terms of your product warranty may rebuild trust in your brand or product’s performance. Following a major recall or significant set of product field failures, customer’s may approach future product offerings with caution. To overcome the buyer’s hesitance extending the warranty terms shifts some of the buyer’s perceived (or actual) risk to the manufacture.
A third reason is purely marketing, which is the next consideration.
Marketing and Buyer Decision Making
People make purchasing decisions in complicated ways.
Price, function, availability, fashion, cachet, and more all play a role in the decision-making process. Individuals likely have very different sets of reasons for the purchase of exactly the same product.
Furthermore, the decision hinges on perceived risk and expected consequence of failure.
The buyer’s perception of a product is built with direct and indirect experience with your product offerings and similar products even from competitors. Another major factor of product perception is created by the marketing and branding.
Marketing teams would like a full long term warranty as it provides support for a durable product. Yet, the cost of warranty when failures actually occur erodes any profits of additional sales with time.
The balance of market share, customer perception, and warranty costs is the heart of decision concerning setting warranty terms.
Product Reliability and Warranty
Warranty is only one cost of an unreliable product.
Market share, brand perception, and the associated lost sales increase of the cost of failure significantly. If a product just works over the duration of the warranty period, the manufacturer does not incur a warranty expense.
Creating and verifying a product has a low probability of failure over a warranty period is expensive. The cost of design for reliability activities and reliability testing are upfront costs that avoid expenses in the future. Yet, recall that warranty expenses are directly proportional to profit.
A dollar spent replacing a product is one less dollar of profit, not counting the potential damage to brand and buyer perception.
A change from a budgeted warranty expense of 3% of net revenue, to 7%, in some product lines would eliminate all profit and may even result in a loss for the organization. A 7% defect rate may not require a product recall (in part this depends on the consequence of the failures and market), yet may negate the business rationale behind creating and selling the product.
Products fail; it is the ability of the team to set a reliability goal and actually achieve it- that helps the entire discussion concerning warranty policy and the setting of warranty terms.
If you know your product has a very small chance of failing over a 5 year period, the setting of a 5-year full warranty may be the right move.
If you, as the reliability engineer or product team, do not know the expected field failure rate, setting the warranty terms becomes wishful thinking.
Summary
Warranty policy within an organization provides a framework to consider the many factors under consideration when establishing warranty terms for a specific product.
In some cases warranty policy is little more than an afterthought, where in some markets setting the right set of warranty terms becomes essential for business success.
Related:
Warranty Prediction (article)
Warranty Management Overview (article)
The Exciting World of Warranty Terms (article)
Leave a Reply