
Failures during product testing and use are a fact of life. Even with the most robust design we can develop an overly aggressive reliability test or find users that dish out punishing treatment, causing product failures. And for designs that are less robust, standard reliability tests and normal users will cause failures, occasionally or frequently depending on the design robustness.
When a product fails, its related to failure of individual components and/or joints between components. When a component or joint fails, it’s because their materials degraded to the point that the component or joint could no longer perform as required.
Root cause analysis and failure analysis
When a failure occurs, a root cause analysis should be performed to identify the event or decision that enabled the failure to occur and implement corrective actions to prevent the failure from reoccurring. Possible root causes are related to many areas such as design decisions, manufacturing problems, product testing conditions and problems, user error, improper maintenance, plain old wear out, and several others.
The first step of a root cause analysis is failure analysis of the product and the failed component or joint. Failure analysis is the engineering process used to determine the failure mode and mechanism of a component or joint and whether a materials deficiency contributed to the failure. It’s a powerful tool for making systematic and effective design and manufacturing decisions that lead to product reliability improvements.
The process includes gathering information about the product, failed components, and failure circumstances, and laboratory analysis of the failed component or joint.
Here’s what can be learned from a failure analysis:
- How did the materials degrade?
- What was the failure mode and mechanism?
- Did the materials meet their composition, microstructure, and property requirements?
- Was the component/joint properly fabricated?
- Does the failure mode make sense for the test conditions?
The information is then used to identify the root cause of the failure. It’s unlikely a root cause will be accurately identified without the information gained from a failure analysis. And it’s likely that problems will linger.
Failure analysis process
Here’s a summary of the failure analysis process I use:
- Review the failure with the engineering team. This includes reviewing photos and drawings of the failed component or joint and discussing the failure circumstances.
- Identify the metallurgical analyses to perform and the samples to be evaluated. Selecting the appropriate metallurgical analyses and samples is important for getting helpful information. And it’s no fun paying for unnecessary analyses.
- Perform the metallurgical analyses and review the data. The analysis information and background information are used to identify the failure mode and mechanism and whether the materials had any metallurgical deficiencies.
- Meet with the engineering team to review the analysis findings and discuss possible root causes of the failure and next steps. While more information may be needed to identify the root cause, the failure analysis is crucial for helping point in the right direction. If a failure is related to the component’s design, the failure analysis findings are used to guide design changes.
Product reliability testing and failure analysis
Many people are familiar with using failure analysis to help determine the root cause of product failures during customer use. However, they are less familiar with using failure analysis during product development, when a product fails reliability tests. It’s unfortunate because many organizations are missing out on the benefits – reduced time to fix failures, fewer repeat failures, fewer repeated tests, and well-informed design decisions.
Instead, what often happens is people have a meeting to brainstorm potential root causes and go off to try to figure things out. Or, a design change will be made to the failed component or joint in hopes of making it more robust. Neither approach is systematic, and it may not fix the problem.
Improving product reliability
There can be many reasons for a failure, i.e. materials, mechanical design, supplier quality, manufacturing process, test conditions, … This information from a failure analysis helps engineering teams quickly identify the cause of the problem and enables well-informed decisions that result in improved product reliability.
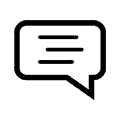
Leave a Reply