
Failure Modes and Effect Analysis (FMEA) is an excellent foundation for Reliability Programs. It is also a stepping stone to build Reliability, Availability, and Maintainability (RAM) models. Here lies the “beauty” of doing Reliability and Maintenance analysis. Whereby information from one analysis can help enhance another analysis.
Definition of FMEAs
FMEA (Failure Mode and Effects Analysis) is a systematic approach used to identify and prioritize potential failures in a system, process, or product. It identifies all the types of possible failures on an asset. This is a fundamental task in every Reliability Analysis. Once the failures are identified, the Risk associated with corresponding failure effects is calculated. This ultimately helps develop plans to detect, prevent, or mitigate critical failures. Doing FMEAs in organizations unlocks a lot of technical knowledge and brings different teams to collaborate. A lot of articles have been written in FMEAs so I will not elaborate further.
When it comes to RAM modelling, the FMEA can bring the following:
- A better understanding of the asset and its components; how they work and how they fail.
- The breakdown of the assets into significant blocks.
- A general idea of critical elements making up the asset or production facility.
FMEA Limitations
Whilst doing an FMEA is a great start to a Reliability Program, it has its limitations. The FMEA looks at asset blocks in isolation. It does not really look at the systems and the interactions of all blocks. By definition, a system is a collection of items whose coordinated operation leads to the output, generally a production value.
The risk calculation in a typical FMEA is somewhat overly simplified. It is related to failures, one block at a time. It does take into account the collective impact especially in complex systems. Additionally, the Risk calculation uses MTBF (Mean Time between Failures) values and Corporate Risk Matrices as shown in Diagram 1 below. MTBF values are misleading and will eventually lead to a flawed analysis. And subsequently flawed decision making.

An example of a Pump FMEA is provided in Table 1 below. The Risk Priority Number (RPN) is calculated at the end. This allows for prioritization of subcomponents or parts. For example, in the derived maintenance strategy, more attention should be attributed to the Impeller (RPN=126) compared to the Seals (RPN=30).
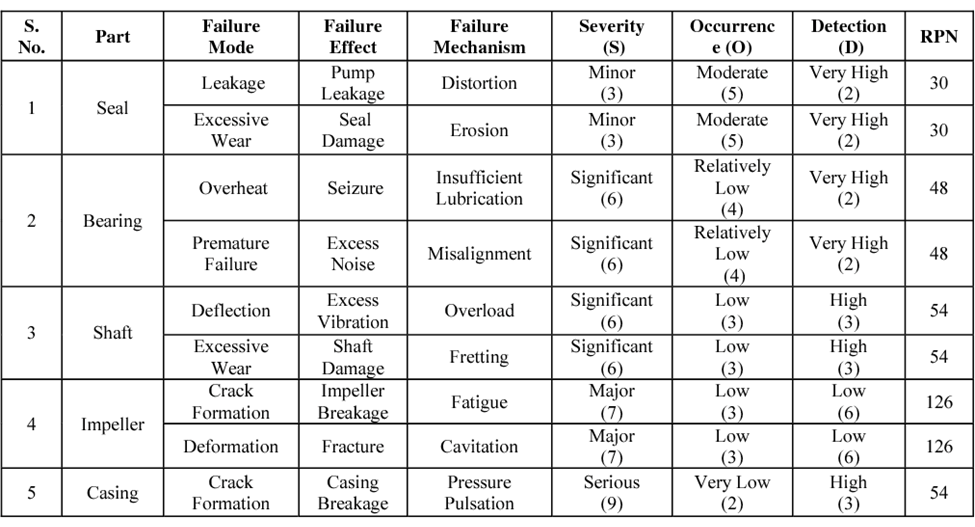
Using and FMEA to build a RAM Model
Using the pump FMEA defined in Diagram 1 above, we can build the RAM model for a Pump. The FMEA, especially Column 2 (Part), is handy to break the pump down into critical components. It speeds up the process, especially if the RAM analyst is not familiar with pumps.
Column 3 (Failure Mode) helps evaluate the consequence. For example, a leakage is a loss of containment that could cause a fire or expensive cleaning work. Therefore, the repair cost is high and considered as such in the RAM model.
The last 6 columns are too generic to be used. The RPN calculation relates to laws of averages and MTBF which are not rigorous Life Analysis methods. Therefore, Life Analysis exercises should be conducted on all the blocks identified.
The RAM model for the corresponding pump is a series model as shown in Diagram 2 below.

In summary, even with its limitations, an FMEA should absolutely be conducted during the elaboration of a Reliability Program. The refinement of this program would come with processes like RAM models and Life Analysis.
Leave a Reply