
Fatigue cracks that originate at inclusions. Stainless steel intergranular corrosion due to chromium carbide precipitates. Low steel toughness because martensite not tempered enough. Low aluminum strength because of excessive grain boundary precipitation. Orange peel due to large grains.
These are examples of how problems with a metal’s microstructure lead to reliability and performance problems. Of course, there are thousands of examples of microstructures that lead to good reliability and good performance.
One hurdle to understanding metallurgy is being able to think small – very small. Less than a millimeter. Less than a micron. And sometimes on the scale of atoms.
Conceptualizing microscopic structures and processes
There are microscopic structures and processes in metals that have large effects on metal properties, performance, and reliability. Being able to conceptualize these structures and processes goes a long way toward understanding the behavior of metals and the effects of mechanical processing and heat treating on metal properties.
I think this is where many people get stuck. The metallurgy terminology doesn’t help. Honestly, it was a struggle for me when I first learned metallurgy. But, after seeing similar concepts covered in different ways in different classes and doing research on metals I began to start thinking small and being able to conceptualize the microscopic structures and processes and how they affect metal properties.
For non-metallurgists, having a decent working knowledge of metallurgy helps them appreciate how it can be leveraged to design better, lower-cost components and quickly solve metal failures and quality problems.
Here’s a brief explanation of some microscopic structures and processes.
Grain structure
The image on the left shows elongated grains in a cold-rolled metal. This grain structure results in the metal having highest strength in the rolling direction and lower strength perpendicular to the plane of the metal. The image on the right shows grains in a metal that was annealed after cold rolling. During annealing, new grains form and grow within the cold-worked grains, eliminating the cold-worked grains.
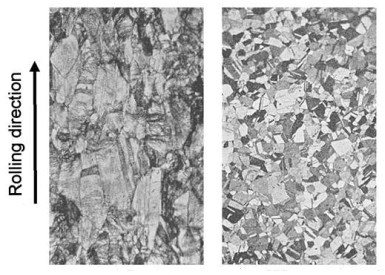
The size of grains after annealing depends on the amount of cold working prior to annealing and the anneal temperature and time. Grain size affects metal strength, formability, toughness, creep strength and other properties.
There’s an additional microscopic structure (dislocations) that affects strength. I’ll leave that discussion for another article.
Phases
The elements present in a metal group together to form one or more phases in the metal. Every phase has a specific arrangement of atoms, is either a mixture of atoms or a compound, and has an exact composition or has a composition within a certain range. A compound is a specific ratio of atoms and has an exact composition. A mixture has a composition within a range.
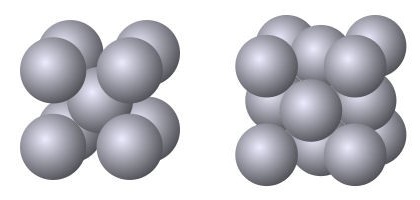
The phases that can form in a metal depend on the metal’s composition. The phases that do form in a metal depend on the metal’s composition and how the metal has been processed.
Within a metal in which different phases can form, the different phases have different properties. By altering the phases present and their relative amounts it is possible to modify a metal’s properties. The phases present and their relative amounts depend on a metal’s composition and the how it was processed, i.e., mechanical working and thermal history.
The image on the left shows a carbon steel that consisted of two phases – ferrite (light-colored) and cementite (dark-colored plates). Ferrite consists of iron atoms with a small amount of carbon atoms mixed in. Cementite is a compound consisting of iron and carbon atoms in a three to one ratio. Ferrite is a low-strength, high ductility material and cementite is hard, strong, and brittle. Together, ferrite and cementite form a composite structure.
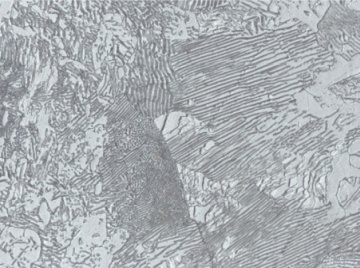
The properties of a steel that consists of ferrite and cementite depend on the relative amounts of each phase present. Also, the spacing of the cementite plates can be modified, causing changes to steel strength and other properties.
Moving atoms
When a metal’s temperature is high enough its atoms move around, jumping from one position to an adjacent position in the metal. This atom motion is called diffusion.
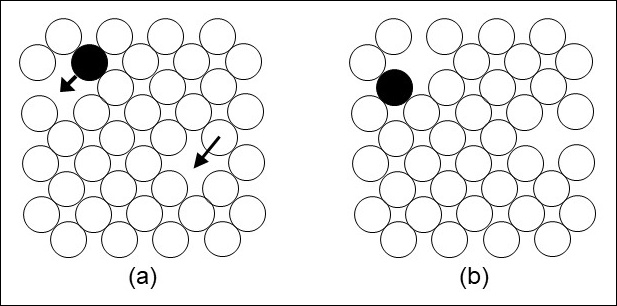
As atoms move around, changes occur to grain structure, phases present and their amounts, and other microscopic structures. The changes that occur depend on a metal’s composition, its temperature, and the time at temperature.
The purpose of any heat treatment is to cause changes to a metal’s microstructure to obtain specific properties. So, for any particular alloy, the proper temperature and time at temperature must be selected and controlled in order for the desired microstructure changes to occur.
It’s not necessary to be an expert
Everyone doesn’t have to be a metallurgy expert. It’s hard enough to be an expert within one engineering discipline. But basic knowledge about microscopic structures, their effects on metal properties, and the effects of mechanical and thermal processing on microscopic structures is important if non-metallurgists want to have awareness of how metals engineering can be applied to design components and solve problems. It’s also important for having productive discussions with suppliers, metallurgists, and metallurgical labs.
I’m not a mechanical engineer but have enough understanding of mechanical engineering concepts and considerations so that I can have productive conversations with them when working on projects. I still depend on their expertise to help fill in my large knowledge gaps.
Interested in learning more about grains, phases, and diffusion? Check out our Principles of Metallurgy online course.
There’s a podcast version of this article that includes more details and discussions about recent projects.
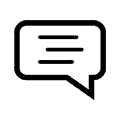
Leave a Reply