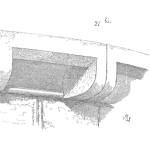
H.L. Mencken, the sharp-witted satirist and critic of early 20th-century American life, once wrote, “For every complex problem, there is an answer that is clear, simple, and wrong.”1 Mencken, born in Baltimore in 1880, was known for his incisive critiques of societal norms and his skepticism of simplistic solutions to complex issues.
Mencken’s wisdom applies to both everyday life and technical fields. His insights are particularly relevant in the engineering, manufacturing, and reliability disciplines, where the temptation to seek easy answers can lead to costly errors. We’ll start with a relatable everyday example before exploring documented cases in engineering and manufacturing that demonstrate the pitfalls of oversimplified solutions.
An Everyday Example: Financial Independence and the Trap of “Just Save More”
A common piece of advice for achieving financial independence is to “just save more money.” This advice is frequently given by financial advisors and passed down as conventional wisdom. On the surface, this seems like a clear and straightforward solution. If you save more, you’ll accumulate wealth over time, right?
However, the reality is more complex. Many individuals face stagnant wages, rising living costs, and significant expenses like student loans or medical bills. Even those who manage to save may find that inflation or poor investment choices erode their efforts. The simplistic advice of “just save more” does not address these broader financial realities.
The complexity of personal finance requires a nuanced approach, including budgeting, investing wisely, managing debt, and planning for long-term goals. Ignoring these complexities can lead to frustration and failure, demonstrating Mencken’s point about the inadequacy of overly simple solutions.
In engineering and manufacturing, the allure of simple solutions can lead to significant problems. Let’s explore some real-world examples where clear and simple answers fell short.
Automation Woes: When Automation Becomes the Bottleneck
Automation is often heralded as the ultimate solution to increasing manufacturing efficiency. The logic seems airtight—automate a process, and you reduce human error, increase production speed, and lower labor costs. However, when automation isn’t properly implemented or fails to deliver as expected, it can quickly become a bottleneck instead of a solution.
In 2023, GM faced unexpected constraints in its battery module production due to supply issues with an automation equipment provider.2 CEO Mary Barra described the situation as “disappointing,” noting that the supplier had struggled with delivery issues, slowing GM’s ability to scale. GM had expected the supplier to meet its delivery commitments, but when delays arose, the company had to take drastic measures to mitigate the impact.
To counteract the problem, GM deployed engineering teams to assist the supplier and even resorted to installing manual assembly lines at its EV plants. This move highlights an important lesson: while automation can be a powerful tool, an over-reliance on it—without adequate backup plans—can create vulnerabilities in launch and mass production.
Supplier reliability is as critical as the automation Itself. An organization may never yield the savings of a failed automation launch before the program naturally ends. Automation should enhance, not replace, manufacturing flexibility. Therefore, manufacturers should integrate automation in ways that allow for human intervention when needed.
Over-Specification of Materials: The Case of Boeing’s 787 Dreamliner
The Boeing 787 Dreamliner provides a well-documented example of the pitfalls of over-specification. To achieve high performance and fuel efficiency, Boeing used advanced composite materials in the Dreamliner’s construction.3 While these materials offered benefits in weight reduction and fuel efficiency, they also introduced significant complexities in safety, manufacturing and maintenance.4,5,6
The use of these advanced materials led to unexpected challenges, including difficulties with quality control and integration, as well as costly maintenance issues. The decision to use high-tech materials, while beneficial in some respects, also highlighted the problems associated with over-specification. Boeing had to navigate these complexities and adjust their approach to address the issues that arose.
Balancing material strength and performance with cost, manufacturability, and other practical considerations leads to optimal design solutions. New materials result in new design and process failure modes. Using a comprehensive material selection process to ensure the chosen materials are suitable for the intended application mitigates the risks of unintended consequences.
The Operations Fix – Too little too late
A common mistake in product development is treating late-stage manufacturing fixes as a substitute for robust early-stage design practices. In a discussion the author had with a mechanical engineering consultant, he described how a client organization expanded its Advanced Operations (AO) teams to compensate for poor design integration. The idea seems clear and simple—if manufacturing teams can compensate for design flaws before mass production, the company avoids costly field failures.
However, this approach guarantees higher costs in the long run and draws resources from AO teams that could be better spent proactively on improvement projects. But unfortunately, AO and lean six sigma teams often function as a corporate immune system, detecting and mitigating design issues after they occur rather than preventing them in the first place. It also reinforces bad habits in early-stage design. And engineering teams may become reliant on AO teams to catch errors rather than integrating first-principles thinking and variation analysis from the start.
Instead of treating downstream customers as a safety net, companies should embed physics-based design and variation analysis at every stage. By shifting focus upstream, engineering teams can ensure that real-world constraints and tolerances are properly defined before manufacturing. This reduces the need for late-stage firefighting and prevents flawed product launches.
Embrace Complexity with Caution
Mencken’s observation about the dangers of clear, simple answers resonates deeply in engineering, reliability, and manufacturing. The temptation to seek straightforward solutions can lead to significant problems when these solutions fail to account for the second and third order consequences of real-world situations.
By embracing complexity and applying critical thinking, we can avoid the pitfalls of simplistic solutions and develop more effective, robust strategies. Mencken’s wisdom serves as a valuable reminder to look beyond the obvious answers and seek solutions that address the true scope of the problems we face.
Ray Harkins is the General Manager of Lexington Technologies in Lexington, North Carolina. He earned his Master of Science from Rochester Institute of Technology and his Master of Business Administration from Youngstown State University. He also teaches manufacturing and business-related skills such as Quality Engineering Statistics,Reliability Engineering Statistics, Failure Modes and Effects Analysis (FMEA), and Root Cause Analysis and the 8D Corrective Action Process through the online learning platform, Udemy. He can be reached via LinkedIn at linkedin.com/in/ray-harkins or by email at the.mfg.acad@gmail.com.
References:
1. Mencken, H.L. 1920. “The Divine Afflatus”. Prejudices: Second Series.
2. Hall, Kalea. July 2023. “GM’s EV ramp-up affected by automation supplier delays”. The Detroit News.
3. R&D Magazine. November 2006. “The Dream of Composites”.
4. Gates, Dominic. September 2007. “Fired Engineer Calls 787’s Plastic Fuselage Unsafe”. The Seattle Times.
5. Gates, Dominic. November 2021. “FAA Memo Reveals More Boeing 787 Manufacturing Defects”. The Seattle Times.
6. Ostrower, Jon. March 2014. “New Boeing Woe: 787 Wing Defect”. The Wall Street Journal.
Leave a Reply