
One failure mechanism that I’m frequently asked about is hydrogen embrittlement of carbon and low-alloy steel. So, in this article I’ll discuss that topic.
Hydrogen embrittlement is the result of the absorption of hydrogen by susceptible metals resulting in the loss of ductility and reduction of load bearing capability. Sustained stress on an embrittled material can result in cracking and fracture at stresses less than the metal’s yield strength.
Embrittlement process
Hydrogen can be absorbed into a metal and diffuse through the grains. This can occur at room temperature and elevated temperatures. The absorbed hydrogen, present as atomic or molecular hydrogen, combine to form small bubbles at metal grain boundaries.
The bubbles build pressure between the metal grains. The pressure can increase to levels where the metal has reduced ductility and enables cracking at stresses lower than a metal’s yield strength. The cracking is intergranular, which means the cracks grow along a metal’s grain boundaries.
Example
An example of failure due to hydrogen embrittlement is shown for a fractured fastener that consisted of zinc plated steel. The fastener fractured about three days after it was installed. There are tensile stresses along the length of an installed fastener.
The right image shows a scanning electron microscope image of the fracture surface. The rocky appearance of the fracture surface is indicative of cracking along the metal’s grain boundaries. The steel became embrittled during the zinc electroplating process.
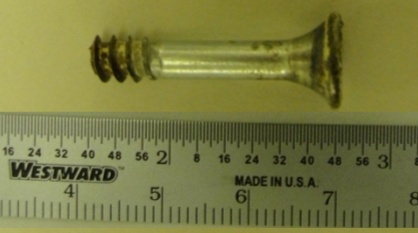
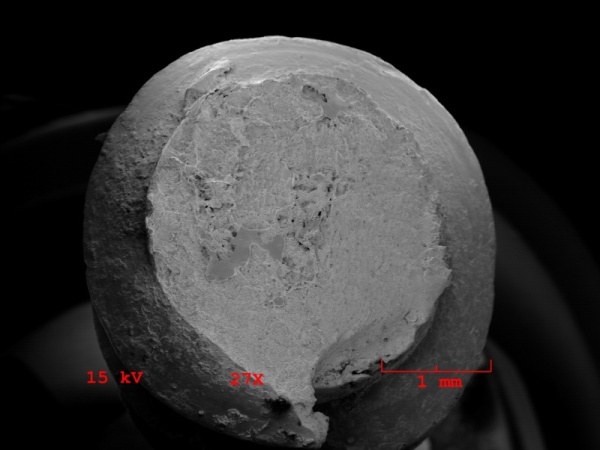
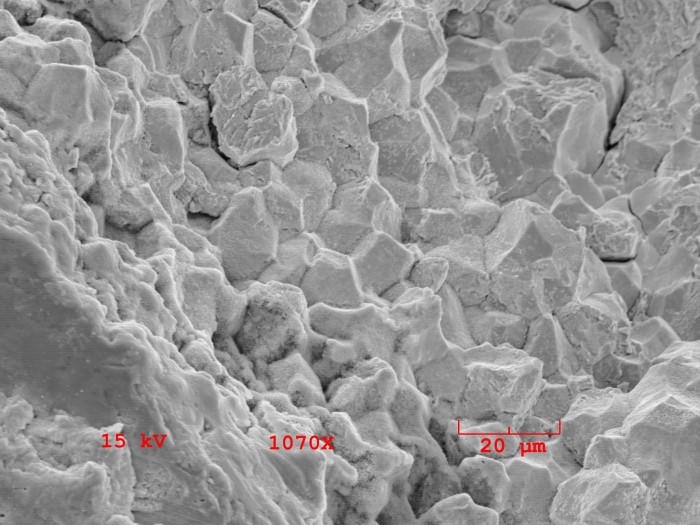
Requirements for hydrogen embrittlement
Three requirements must be met for hydrogen embrittlement to be a concern:
- A susceptible material
- Exposure to an environment that contains hydrogen
- Sustained tensile stress
Residual stress can contribute to the total tensile stress on a component and in some cases is sufficient to cause cracking.
High-strength steels are susceptible to hydrogen embrittlement. This includes steel with tensile strength greater than 140 ksi (1,000 MPa) or hardness greater than 30 HRC.
Hydrogen absorption can occur during various manufacturing and assembly operations or during component use. Processes that result in component exposure to hydrogen include phosphating, acid pickling, and electroplating. During use, hydrogen exposure can occur during metal corrosion, chemical reactions of metal with acids, or with other chemicals notably hydrogen sulfide in sulfide stress cracking.
Preventing hydrogen embrittlement
Steps can be taken to avoid hydrogen embrittlement of carbon and low-alloy steel components exposed to hydrogen. They include:
- Bake the metal after processes that involve exposure to hydrogen
- Use lower strength steels
- Reduce residual and applied stress
The baking temperature is often 190 – 220 °C and the time depends on the steel strength. During the bake hydrogen diffuses out of the metal. The bake process must be performed within a few hours after the hydrogen exposure occurs. The bake will not be effective if too much time elapses between the hydrogen exposure and the bake. ASTM standards that specify the baking process to use are available.
Using lower strength steels, reducing residual stress, and reducing the applied stress may be the best options when hydrogen absorption occurs while a component is in service. One way to reduce residual stress is to select an alloy that enables using a less aggressive quench during the strengthening heat treatment. Applied stress can be reduced by increasing a component’s cross-section.
Selection and control
Hydrogen embrittlement and its causes are well-understood, and several approaches exist to prevent its occurrence. As discussed in a recent article, selection and control are important for reliability.
When designing components for which hydrogen embrittlement is a concern, it’s important to test the components to verify that they are not embrittled after fabrication is complete and/or that they do not become embrittled during use. It’s also important to verify that the people responsible for surface finishing high-strength steel follow proper procedures to prevent hydrogen embrittlement.
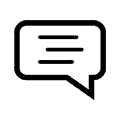
Leave a Reply