
When designing components consider fatigue or stress corrosion cracking. It’s important to be cognizant of the residual stresses in the component. Understanding residual pressure and its sources is important when making decisions about a component’s shape, features, alloy, and fabrication process.
Fatigue and stress corrosion cracking require the presence of tensile stresses on a component. When residual presures are tensile they add to the applied tensile pressure, reducing the life of a component. In fact, components sometimes fail due to stress corrosion cracking when residual stress is the only source of tensile stress.
Locked-in stresses
Residual stresses are locked-in elastic pressures present in a metal that is free of external forces. Elastic pressures are less than a metal’s yield strength and cause elastic deformation of the metal. The deformation is associated with stretching of the bonds between a metal’s atoms.
Residual stress arises from:
- Non-uniform plastic deformation
- Non-uniform contraction during cooling
- Phase transformations during heat treating
- Surface treatment, e.g. carburizing, coating, shot peening
Regardless of the origin, residual stress can be tensile or compressive. In many cases, tensile and compressive residual forces can co-exist within a component.
Effects of residual stress
Considering only applied and residual stresses, the total pressume on a metal is a sum of the applied stress and the residual stress. Tensile residual stress adds to an applied tensile stress and compressive residual stress subtracts from an applied tensile stress.
So, residual stresses can be harmful or beneficial, depending on whether the stress is tensile or compressive.
For fatigue and stress corrosion cracking, the stress at the surface of a component is important. Surface residual compressive pressure reduces the effects of applied tensile pressure, improving resistance to fatigue and stress-corrosion cracking. Surface tensile residual pressures add to an applied tensile pressure, reducing resistance to fatigue and stress-corrosion cracking
Non-uniform deformation
Residual stresses arise when metal plastically deforms and the deformation is not uniform throughout the metal’s cross-section or along the length of the metal. This can occur during room temperature metal shaping processes such as bending, drawing, and rolling.
When a metal undergoes permanent deformation a portion of the total deformation is elastic deformation. When the force causing plastic deformation is removed, the metal tries to relax the elastic portion of the deformation. If the plastic deformation is non-uniform, all or part of the elastic portion of the deformation remains because adjacent areas of the metal prevent complete relaxation of the elastic deformation (strains). The unrelaxed elastic deformation (strain) is the source of residual stress.
Consider a metal item that has been bent. On one side of the bend the bending pressures are tensile and on the other side they are compressive. After removing the external force, the two regions prevent each other from completely relaxing their elastic stresses. As a result, residual compressive and tensile pressures remain.
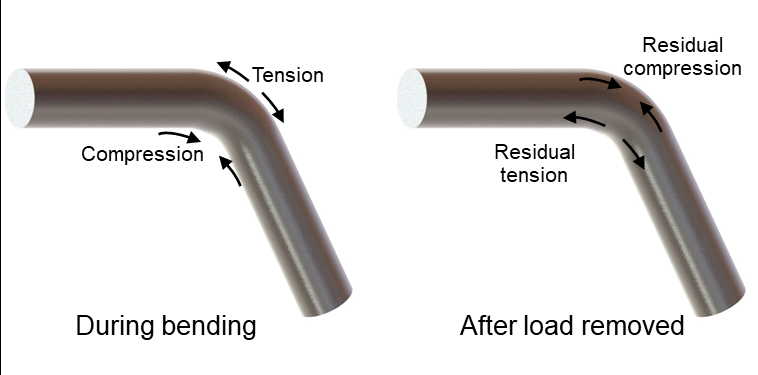
Residual stress due to temperature variations
When a metal cools metal from elevated temperatures, the outer portion of the metal cools first and contracts, compressing the hotter inner metal. As the inner portion of the metal cools, the metal tries to contract, but the already cooled out portion constrains movement. Consequently, the inner portion will have a residual tensile pressure and the outer portion of the metal will have a residual compressive forces. This occurs during heat treating and welding.
Residual stress due to phase transformation
A phase transformation is a change in the metallurgical phases present in an alloy. The transformation from austenite to martensite in steel during through hardening is a phase transformation. Volume differences between the final and initial metallurgical phases causes expansion or contraction of the metal.
For phase transformations that occur during cooling from an elevated temperature, the outer portion of the metal cools first and undergoes the phase transformation before the metal’s interior. As the interior of the metal cools the volume difference between the initial and final phases will cause the interior metal to change volume. However, the volume change of the metal interior will be constrained by the cooler outer layer of metal that already transformed. As a result, residual pressures will appear within the interior and exterior portions of metal.
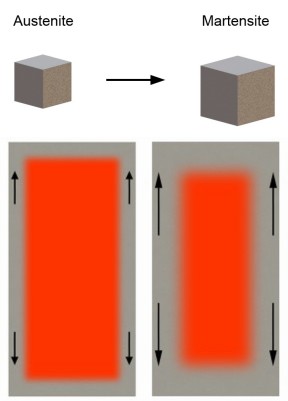
Controlling residual stress
One may use mechanical treatment, stress relief heat treatment, control of heat treating processes, and alloy selection to control the type and magnitude of residual stress in a component.
To induce compressive residual stress at the surface of a component consider using mechanical treatments such as shot peening, light cold rolling, stretching, and small amounts of compressing.
Metal yield strength decreases as its temperature increases. So, you may heat metals to temperatures that relieve some or all the elastic pressures. At the elevated temperature the metal’s yield strength is less than some or all the residual stress and the metal undergoes microscopic plastic deformation. Thus, releasing at least a portion of the residual pressure.
From a component processing perspective, one may minimize residual stresses. One approach is by using reduced cooling rates to reduce temperature variations throughout a component. Thus, allowing for phase transformations to occur more uniformly throughout a component’s cross-section. Also, select alloys that permit a slower cooling rate during heat treating. And, still getting the desired phase transformations to occur. For example, for carbon steel components through hardened using the quench and temper process, low-alloy carbon steels enable the use of slower cooling rates compared to plain carbon steels.
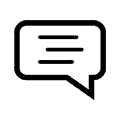
Yes. Please tell more: Miner’s Law, crack initiation, Paris’ Law, load-sharing, ??? THis is a big deal in piping reliability under pressure. https://www.osti.gov/biblio/10162360-theoretical-user-manual-pc-praise-probabilistic-fracture-mechanics-computer-code-piping-reliability-analysis#:~:text=PRAISE%20is%20an%20acronym%20for%20Piping%20Reliability%20Analysis,PRAISE%20has%20a%20deterministic%20basis%20in%20fracture%20mechanics.
Those are all important topics. I can discuss fatigue crack initiation. The others are probably too much detail for this site and are outside my expertise.