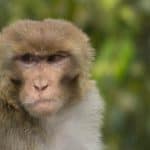
Who are you fooling with MTBF Predictions?
All models are wrong, some are useful. ~ George E. P. Box
If you know me, you know I do not like MTBF. Trying to predict MTBF, which I consider a worthless metric, is folly.
So, why the article on predicting MTBF?
Predicting MTBF or creating an estimate is often requested by your customer or organization. You are being specifically asked for MTBF for a new product.
You have to come up with something.
The available options include the Mil Hdbk 217, similar standards, IEC 61709 and VITA 51.2. There may be others. These parts count approaches are flawed and should not be part of your reliability plan.
Mil Hdbk 217 is out of date.
The Mil Hdbk 217F Notice 2 was published in Feb 1995. There is work to update the standard to the G revision and is making progress. It’s not out yet (as far as I can determine), and it promises to incorporate more failure mechanisms and physics of failure approaches.
We’ll see.
In the meantime, do not use Mil Hdbk 217, as it is outdated.
IEC 61709 Physics of Failure Reliability Prediction limited scope
The IEC 61709 Rev 2.0 published in 2011 is major step in the right direction. While limited in scope and using a simplistic model, it provides a means for vendors to conduct and report product testing that users may convert to their specific use conditions.
This is wonderful.
The standard still uses failure rates and modifications as the structure. You will notice familiar equations for electrolytic capacitor life and the Arrhenius equation, and a many more.
The equations and data used for fitting parameters are conservative. The idea, in part, is to bridge the 217 approach and physics of failure approach.
Like many IEC standards, it doesn’t provide sufficient background and references for formulas and fitting parameters. It also doesn’t discuss the many underlying assumptions needed to properly apply the formulas.
VITA 51.2 Physics of Failure Reliability Predictions is better
Now we’re getting there.
Good stuff in this document. More models and it includes some of the how and why to apply, including assumptions. While not a full textbook, it make a major step forward.
Downside, not widely accepted in the contracting world. The Mil Hdbk’s and IEC standards seem to dominate. The VITA 51.2 is good work and should start to become the standard going forward.
We can hope.
Yes, it takes work. The best way to predict the future is to wait and measure it. Often, we do not have time for this approach.
We need to make decisions today about design and assembly decisions that may impact product performance 20 years in the future. Even 5 years is difficult.
Starting with an outdated model is sure way to be wrong. Using a current physical of failure model may require some thinking, additional data and a bit of research.
It is worth it?
What decisions are you making and are they important? If so, then use the best technology available. It may take some work.
So be it.
How do you make your reliability predictions? What are you being asked to forecast? How successful are you?
Fred you make some very good points, especially about the inaccuracies and invalidity of Mil handbook book 217 (and its progeny).
Predicting the future, including failure rates of electronic products with no moving parts, would be extremely valuable if it could be done. The problem is more fundamental that accurate models of intrinsic physics of failures of components. If only reliability engineers reviewed and analyzed the root cause of failures, they would see that the cause of the vast majority of failures in electronics, especially those that occur during the warranty period and in the early years are rarely due to intrinsic “wear out” failure mechanisms, which are mechanisms that can be modeled for usable life estimates. The causes of failures are mainly due to errors in manufacturing processes, overlooked design margins, or by use errors of customers. Compounding the challenge of prediction is that it requires many broad assumptions about average end use stress environment, use profile, and capability and consistency of the manufacturing processes at many levels of assembly. You have recently published that basing decisions on assumed averages will provide wrong answers and I certainly agree .
The only way this could be shown to be true is by having many electronic companies disclose the actual causes of most of their failures in the early years of use. And this is the continuing dilemma, no electronics manufacturer or design company will ever release the actual causes or rates of failures that their products have seen in the field (without a court order). Because of the lack of distributed knowledge on causes of real warranty failures the belief and decades long delusion that the rates of failures of electronics with no moving parts can be predicted. Most electronics do not fail. Instead most are turned off because the replaced by something much more capable with more features or benefits.
Accurate and useful predictions cannot be done for most causes of early life failures in electronics and we must educate those that still believe it can be and keep asking for MTBF predictions. Most of the resources for reliability development of electronics should be on finding causes of unreliability based on real data from the field.
Hi Kirk,
I consider three classes or sources of product failures, all of which we have an interesting in estimating.
Supplier and assembly faults
Overstress faults
Wear out faults
As any product that has been out there for some time experiences is a rate of occurrence of all of these types of faults. Sure different product may have a different mix, yet that doesn’t mean we shouldn’t or can not create an estimate of failure rates.
The article here talks about the standards driven predictions and you’re right in pointing out they do not consider two of the three sources of failures.
Cheers,
Fred
Hi Fred,
do you know where I can find the VITA 51.2?
Thanks a lot,
Valeria
You can try via https://www.vita.com/page-1855315 cheers, Fred
Hi Fred,
unfortunately this page doen’t exist. Could you please update it?
Thank you
Petr
The VITA standard are for sale or free for VITA members at https://www.vita.com/Standards scroll down to find the 51 series