
Any product is an assembly of components comprised of different materials. The reliability of the product depends on the reliability of the materials – their ability to withstand exposure to the use conditions without degrading to the point that the component or joint stops performing as needed.
There are two approaches for evaluating the reliability of materials: 1) product testing and 2) materials testing. Both involve exposing test samples to actual or simulated use conditions and evaluating the response of the test samples as a function of the amount of exposure to the test conditions. For example, exposure to thermal cycling between -40 and +40 °C or exposure to salt spray.
Product testing and materials testing each have advantages and disadvantages that are important to consider when deciding on the approach to take for gathering data about materials reliability, and for managing risks to meeting product development deadlines. I’ll discuss the differences between both approaches and their advantages and disadvantages.
Product testing
For product testing, the test samples are the product. The purpose of the tests is to determine whether the product can meet its performance requirements after exposure to the test conditions. For many tests, the performance characteristics of the test samples are also measured at intervals during the exposure.
The data obtained from product testing is pass or fail. Test samples pass if they satisfy the product performance requirements after test exposure. For some products, information about changes in product performance as a function of amount of exposure to the test conditions can be obtained.
If the test samples pass, the design team infers the materials are suitable for the application. If the test samples fail, then the design team must determine the cause of the failure and correct it. In many cases, failed later stage tests must be repeated after addressing the cause of the failure, potentially delaying the product’s launch.
With product testing as an approach to assessing the suitability of materials, the advantages are
- Evaluation of all components and joints at one time. So, the testing is efficient.
- Improved likelihood that all interactions between components and joints that can cause degradation do occur. See Design for Reliability – Identifying Stressors.
The disadvantages with using only product testing to evaluate the suitability of materials are:
- Risk of test failure. Root cause analysis, redesign, and retesting due to failed components or joints diverts engineering resources from other products and can delay product launch.
- Little information is obtained about the materials. If the materials are more reliable than necessary, the cost to make the product might be more expensive than necessary. If the materials are just reliable enough to pass testing, typical variations in the materials may lead to product failures. I’m working on a project right now that involves 3% field failures because of variations not identified during testing.
- Only one material option is considered for each component. The cost and effort required to build and test samples typically makes it unrealistic to evaluate more than one material option for a component. This is a barrier to assessing alternate materials that offer potential costs savings or improved reliability or performance
Materials testing
For materials testing, test samples can be individual components, individual joints between components, sub-assemblies, or just the materials being considered for components or joints. Many times, materials testing is performed without using the exact components that will be used in the final product.
Here are two examples of materials testing:
- Adhesive joint between two metal components and concerns about loss of adhesion and corrosion near the joint when exposed to hot, humid conditions and corrosion conditions. Make test samples from stock metal of different alloys and using different adhesives. Test data will include degree of corrosion and joint strength.
- Coating wear resistance and adhesion for high temperature application. Coat substrate metals with different coatings and perform wear testing. Expose test samples to cycling between +25 to +200 C and then perform adhesion testing.
Materials testing is not pass/fail. The properties and characteristics of the materials and the test samples are evaluated before and after exposure, and often at intervals. The test data are used to quantify the effects of the exposure on materials’ properties and characteristics and on test sample performance. The data is then used to guide component and joint design decisions, improving the likelihood of passing product testing.
The advantages of materials testing are:
- Does not require building the entire product to assess materials. Degradation and reliability information can be gathered in parallel with other product development activities. Data is then ready for the design team when it is time to select materials for product testing. The data improves the probability of selecting materials that enable passing product tests the first time.
- Can evaluate several materials options and/or suppliers of materials at one time. Evaluating more than one material option and/or supplier at one time enables design teams to consider a range of materials options, improving the likelihood of finding a material that meets the design requirements for a component or joint.
- Test data is quantitative. This enables comparison of materials based on material properties, characteristics, reliability, and cost. It also enables development of physical models for predicting the degradation behavior of materials. The information can be used for material selection decisions for future products based on reliability requirements, enabling faster and better-informed design decisions.
The overarching benefit is the information will help design teams design components and joints that pass product testing, and possibly helping to reduce product development time.
The only disadvantage of materials testing is the extra engineering resources required to perform the tests. However, the reduced design times, increased certainty of passing product verification tests, and increased number of materials options are all benefits that justify the investment of time and money.
Test materials for all components and joints?
It’s usually not necessary to perform material reliability tests for all the materials used in a product. Design teams should focus on critical components and joints. Failure Modes and Effects Analysis (FMEA) can be used to identify the components and joints that pose the greatest risk to the reliability of a product and focus on those.
A powerful approach for assessing materials
Materials reliability testing is a powerful approach for assessing material options for components and joints and gathering information that can be used to guide product design decisions. It takes time and effort to set up the testing, but the benefits of improved engineering decisions, optimized designs, and passing product reliability testing the first time are worth the expense.
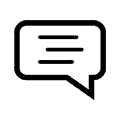
It takes time and effort to set up the testing!
Yes it does. But how much time and effort is spent chasing down the root cause of product test failures, fixing the problem, and retesting? And if an engineering team plans (and hopes) for tests to pass the first time, who will do the work?