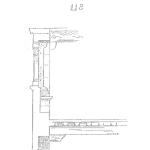
Preventive maintenance is a proactive approach used by industries to ensure the longevity and optimal performance of their assets. It involves regular maintenance tasks such as cleaning, lubrication, parts replacement, and equipment repairs to prevent unplanned downtime and costly breakdowns.
There are several types of preventive maintenance, including:
- Time-Based Maintenance (TBM): This type of maintenance is performed at regular intervals based on a set schedule, regardless of the equipment’s condition.
- Usage-Based Maintenance (UBM): This type of maintenance is triggered by the actual utilization of an asset. It takes into account the average daily usage or exposure to environmental conditions.
- Condition-Based Maintenance (CBM): This type of maintenance involves monitoring the actual condition of the asset to decide what maintenance needs to be done.
- Predictive Maintenance (PdM): This approach involves using predictive maintenance tools such as sensors, software, and data analytics to monitor and analyze equipment performance. It helps organizations gain better insight into the “symptoms” that suggest the need for repairs.
- Risk-Based Maintenance (RBM): This type of maintenance takes into account the risk of failure and the consequences of failure to prioritize maintenance activities.
Here is a table summarizing the different types of preventive maintenance, their explanations, areas of use, and examples from different industries:
Focusing on predictive maintenance, it is a game-changer for any industrial enterprise that relies on physical equipment. Predictive maintenance analytics incorporates machine learning and statistical algorithms to monitor and analyze equipment conditions. By using powerful tools to monitor and analyze equipment conditions, companies can better identify the warning signs of equipment failure and develop a proactive approach to maintenance. Predictive maintenance can improve productivity by as much as 25 percent, cut maintenance costs by 25 percent, and reduce breakdowns by 70 percent.
It requires the use of machine learning techniques to explore and analyze large and complex data sets, often referred to as big data. This data can be collected from various sources, including sensors, maintenance records, and parts replacement history.
In conclusion, preventive maintenance, with its various approaches, plays a crucial role in maintaining the reliability and longevity of equipment, with predictive maintenance standing out due to its data-driven and proactive nature.
Leave a Reply