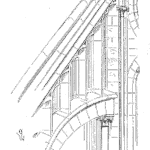
Is it possible for an individual to ‘do’ DFR? Is design for reliability something, like a specific technique, that is DFR?
What is DFR and how would you recognize it if it was occurring? Like meditation, nearly anyone can strike a pose that appears similar to someone in deep meditation, yet can you tell by observation if they really are mediating? Probably not. The same is true for an organization or person that declares they are doing DFR. Maybe they are or maybe not.
What is DFR?
Design for Reliability (DFR) is a collection of tools and techniques that address the reliability aspects of a design. The tools focus on creating a robust product and one that meets the reliability objectives.
Technically one person could perform all the various activities. They could calculate the safety factors built into the design, estimate system life and explore for weaknesses. It would be a challenge just to accomplish all of the various tasks during the product development phase.
Would that be a DFR program? No, not really, as just accomplishing a range of tasks in not sufficient to impact the resulting system reliability.
Beyond the specific tasks, DFR is decision making within the organization. Keep in mind that the resulting reliability is designed into the product. The process of product design involved thousands and thousands of decisions, each one affecting the reliability performance.
The decisions by each member of the design team include to some extent an element of reliability. A DFR program that enables each decision to consider the impact on reliability is an effective program.
What can we observe to see DFR in action?
The various tools and techniques
- Increase awareness of how decisions impact reliability
- Reveal connections between design elements of reliability
- Provide feedback on expected reliability performance
- Expose weaknesses that limit reliability
- Confirm design strength and robustness
The individual tools provide value directly, yet in combination and distributed across an organization a DFR program enhances the capability of the design and development team to create a reliable system.
When the decisions related to product design include reliability factors, decisions made by everyone in the team, then you are doing DFR. When the team discusses design aspects that naturally includes reliability that is DFR. Anyone raises meaningful reliability questions and pursues the appropriate experiment or analysis.
As with meditation it is the process, how we think and make observations, that matters. The range of tools and techniques should change for each circumstance. Practicing and mastering the tools takes time, yet the gained wisdom allows us to guide the organization to create robust and reliable systems.
Although Six Sigma and Design For Six Sigma (DFSS) have been quite successful in achieving higher quality, reducing variation and cutting down the number of non-conforming products, the methodologies are primarily focused on product quality and many organizations are starting to realize that they do not adequately support the achievement of high reliability. Therefore, these organizations are starting to put more emphasis on the separate, although often complementary, techniques of Design for Reliability (DFR).
Design for Reliability guidelines include the following:
• Design based on the expected range of the operating environment.
• Design to minimize or balance stresses and thermal loads and/or reduce sensitivity to these stresses or loads.
• De-rate components for added margin.
• Provide subsystem redundancy when possible.
• Use proven component parts & materials with well-characterized reliability.
• Reduce parts count & interconnections (and their failure opportunities).
• Improve process capabilities to deliver more reliable components and assemblies.