
What is Maintenance Optimization?
Maintenance Optimization is a Reliability Engineering process which helps organizations avoid unnecessary spend whilst minimizing the risk of a costly failure. Planned replacements or inspections detect or prevent failures for components or systems with increasing failure rates. This improves asset reliability and helps control maintenance spend. Increasing failure rates refer to having a Weibull distribution shape parameter Beta (β) greater than one. Specifically, the failure rates located in the right section of the bath tub curve as shown in Diagram 1 below. Admittedly, the life characteristics have to follow a Weibull distribution in this case.
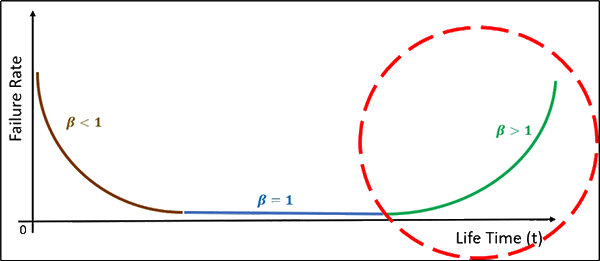
The typical but not optimal preventive maintenance strategy would be to replace an aged or deteriorated component at a given time interval in order to reduce the risk of failure. However, the best approach is to identify the optimal replacement time interval when the cost of maintenance and risk of failure is the lowest possible. An optimal time interval exists if the failure rate increases with time as in the above-mentioned case. In addition, the cumulative cost of failure over time is much higher than the cost of a scheduled replacement. Diagram 2 below illustrates the optimum replacement time point as well as the required inputs.
Another way to see to maintenance optimization is risk minimization. In the above example we are specifically attempting to minimize the financial risk. Note that the risk is never nil; it is at its lowest possible value.
Periodic replacement versus periodic inspection
As an alternative to periodic replacements, periodic inspections can be performed to detect upcoming failures. Should advanced deterioration be detected, components are replaced before they fail. If the failure were to occur, it could be catastrophic. For example: a crude oil pump fails around 2 o’clock in the morning in an unmanned location. It spills a large amount of flammable liquid causing an explosion and fire.
Inspections are often in the form of Condition Based Monitoring or CBM tasks. These tasks will evaluate if a device is working properly. Or identify the condition it is in. CBM can detect signs of impending failure due to degradation. Such as corrosion, crack, vibration or heat. This level of detection would be impossible with our human senses such as touch, eyesight or hearing. When detected by our senses, it is usually too late. Another advantage of CBM is that it is non destructive and does not require the monitored equipment to be offline. This reduces production interruption and revenue losses.
Therefore, on one hand we could chose to replace at specific intervals (sometimes indiscriminately) without inspecting first. On the other hand, we would inspect periodically and then replace only if degradation is beyond a certain threshold. But which approach is more economical? A maintenance optimization exercise will help figure this out.
Selecting the best Maintenance Strategy
As mentioned above, we used the optimization calculator to calculate the following:
- Planned replacement interval
- Planned inspection interval
- The best above-mentioned option where the financial risk is minimized
The example in Diagram 3 below applies to a roller bearing assembly. This article goes in tandem with a presentation I shared at the LRVS 2024. We have included an additional cost which is the cost of inspection.
The optimization curves provide the following information:
- The optimized planned replacement interval is every 31 months
- The optimized planned inspection interval is every 5 months
- The planned replacement minimum is higher than that of the planned inspection. Therefore, planned inspection is recommended.
More information on this calculation and is provided in Reliawiki.com. In summary, Maintenance Optimization calculations help define the most cost effective maintenance strategy. In other words, what action we take and how often we take the action. It can lead to significant savings in the maintenance department. It also frees up maintenance resources. If a task frequency is reduced (i.e. we do it less often), then maintenance technicians can focus on other tasks.
Leave a Reply