
The mining industry in Australia has for some time been plagued by high turnover in its skilled maintenance workforce. The tough lifestyle and remote/regional locations are some of the main contributing causes, and have been for years, however other industries of employment offering competitive wages and a better lifestyle have in the recent years pulled the workforce from mining, leaving a void of labor numbers behind that have proved difficult to fill.
The common query, “How do I keep equipment reliability up, even with high turnover?” prompts a standardized response from most maintenance professionals – proceduralize the maintenance system to reduce variability and maintain consistent output. However, while this approach bears truth, it overlooks a substantial aspect…
That overlooked aspect is the multi-dimensional nature of human interaction within the maintenance system. While procedures are necessary for ensuring consistency, they cannot function as stand-alone solutions. In reality a good maintenance model incorporates key “foundations”, a starting point, a finish point (the maintenance/reliability goals) and of course, the driving force to get us there (Continuous improvement). This all is best characterized in a model developed by Gerard Wood in his book: “Simplifying Maintenance”)
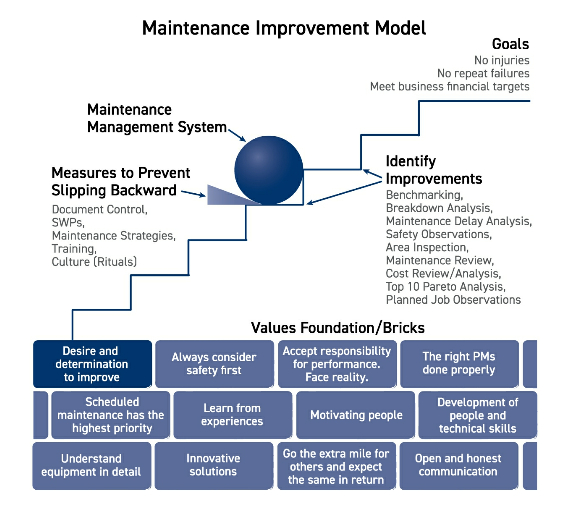
You see, this model is what I call a complete model, and we can spend all day going into detail, but the aim of this article is to tackle the deterioration in reliability that comes with maintenance work force attrition. By looking at the model, which foundations and working forces will be affected by high turnover?
Well, lets see below:
- Foundational
- Understand equipment in detail
- Open and Honest Communication
- Development of people and technical skills
- Desire and determination to improve
- Backstop measures:
- Culture
- Training
- Driving forces:
- Planned job observations
- Reliability Engineer Turnover
I’ll let you in on a little secret- maintenance employee turnover is difficult to control, especially when the root cause is an industry/economic problem rather than a site or company specific issue.
The best way to tackle this is of course by planning for the inevitable attrition cycle, and retaining as much culture and knowledge IN the maintenance system rather than specific people.
This may sound a little confusing, so let me elaborate…
A fitter who has been working on the same type of haul truck for the last 15 years will have gained a deep knowledge on how to maintain the machine. Unwritten knowledge that lies outside the written domain of OEM Manuals and Site procedures. Knowledge, such as understanding which components degrade faster, how dust gets into certain areas causing premature wear, and how to prevent the conditions that cause failures. This experience-based understanding is a significant value that goes beyond reading a manual.
So how does this knowledge get passed from the person to the maintenance system for other to absorb?
Comprehensive Training Programs & Knowledge Management Systems
Rather than relying on individual experiences, develop a robust training program that includes both the written domain of OEM Manuals and the unwritten knowledge that comes from hands-on experience. Incorporate real-world scenarios and hands-on learning to ensure that knowledge is standardized and accessible to all.
Create databases, wikis, or regular knowledge-sharing forums where mechanics can document insights, nuances, and best practices. Encourage a culture of continuous learning and collaboration so that expertise remains within the system, regardless of staff changes.
This of course needs to happen while you still have experienced individuals currently in your maintenance department- no use if they’ve left! Most of these items will require some proactivity, and of course, investment of time and resources.
Cross-Training and Specialization
Develop cross-training initiatives that ensure flexibility within the team, coupled with some level of specialization. While every mechanic might not specialize in a single machine, having specialized roles ensures that expert-level understanding is not lost. For example, split the maintenance workforce into “Heavy Crew” (Equipment such as Excavators, Drills, Loaders etc., HME Crew (Haul trucks, Service trucks, Water carts), and Ancillary Crew (Dozers and Graders). By giving workers some sort of specialization, they build up knowledge around equipment nuances much faster, and can pass this knowledge on further to other. Almost like an infection. This sort of setup also paves the way for encouraging ownership of equipment maintenance performance. Couple this with incentives and you’ll see your machine reliability improve substantially.
Preventive Maintenance Practices
By retaining insights on how machinery fails, develop preventive and predictive maintenance schedules that reflect the collective knowledge of experienced staff. Remember, the FMECA’s we develop when we acquire assets is not a fixed tool- It’s supposed to evolve and change as time progresses, until it’s tailored to how the machine operates and the roughness of environment it’s subjected to.
A system needs to be in place where component failures/ changeout data makes it from the workshop floor to the Reliability Engineer. Changed a component out cause it reached hours? Great, a component change-out form needs to be in the process, as this data will affect the Weibull analysis for this part, and subsequently the changeout tactic. Changed a component out that failed prematurely? Again, the hours need to make it back to the Reliability Engineer, but the part should also be put aside for a failure analysis by a lab or third party. It goes without saying that this process needs to be robust and ingrained within the workshop floor.
Build Relationships with Manufacturers
When it comes to equipment knowledge, your OEM is your best friend. Don’t be fooled though- if your employee attrition is due to an industry problem, then I’ll be you 50 bucks that your OEM is also suffering from the same. Your customer service rep today might not be here next month, but usually they have robust systems in place to keep deep expertise in their equipment.
Make sure you keep a strong relationship with your OEM and involve them in most decisions. You’d be surprised how many times I’ve been pondering for days on a the cause of a component failure only for it to be answered by a quick “Oh yeah, it’s just this that’s the issue” response from a coffee chat in the lunch room from our CAT rep.
Consider Human Factors
If your industry is struggling to retain people, its going to be no surprise that you must ensure people WANT to work at your operation instead of anyone else’s. Higher salaries and benefits will get a person through the door, but won’t keep them. You can pay me as much money as you want, but if I dread going to work every single day I won’t last very long right? Note: This does not mean Salary and Benefits don’t matter! You must always stay competitive in this area.
I recently has a mine inspector visit, and he took some time to interview the workforce on some hazard awareness, but he also took the time to ask them how they liked working at our mine. The feedback was ended up being quite positive, with most employees enjoying their time here and looking forward to their work day. They’ve got a good bunch of colleagues and supportive management.
Fostering a culture of mutual respect, where everyone’s inputs are seriously considered and people are encouraged to speak up and make the maintenance department a better place- that’s how you start fostering a great workplace culture. Giving people ownership over the machines they work on, and incentivizing great performance goes a long way as well.
Although this article was around what to do when people leave, the a core lesson is to prevent people from leaving in the first place as much as possible. Do not let talent walk out the door!
Leave a Reply