How Building Reliability Into The Equipment Design Will Dramatically Improve Your Profitability.
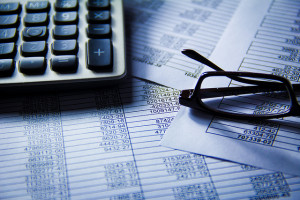
Does your team procure, setup and put into operation equipment with a single focus on reducing the initial capital expenditure?
Do you work with your equipment suppliers to fully specify the equipment’s functions, performance, and reliability? Maybe not the reliability?
Do you track your spare parts, uptime, and related costs of equipment downtime? Most organization do as it is a major element of equipment operation.
The purchase price of an asset is only one element of the total cost of ownership. Yet, many organization focus on the purchase price (and start of production date) instead of the cost of ownership over the equipment’s full life cycle when making purchase decisions.
In the article, Where Does maintenance Fit into Reliability, by James Kovacevic, he discusses the cost of incurred by poor reliability and the necessity for getting the system design correct at the start. In this article let’s explore the concept and what makes up ‘life cycle costing’.
Avoid Making Costly Mistakes
This can be a fatal financial mistake as the reliability of the equipment is built into the design of the equipment. This called the inherent reliability. Once the equipment is designed and installed, there is little the maintenance can do to improve the reliability performance or uptime.
New equipment may provide new capability, improve efficiency or enhance product quality, yet this only happens if the equipment operates. Once installed the maintenance team has very limited ability to redesign, rework or enhance equipment to improve its reliability performance.
Items to Consider Including
Consider a simple example, a ball-point pen. Let’s say it cost $100 to purchase. It is comfortable to hold, writes well, and is stylish. If the replacement ink cartridge cost $5 and last a couple of years of daily use that would be a reasonable life cycle cost experience. On the other hand if the cartridge cost $50 and lasted only a month I may want to find a new pen soon.
There are many other elements to the life cycle cost including:
- Manufacturing costs
- Purchase price
- Transportation costs
- Installation costs
- Start up costs
- Training costs
- Maintenance costs
- Repair/Spares costs
- Replacement/Warranty Costs
- Decommissioning costs
- Recycling costs
Each cost, including initial purchase price is to some extent controlled by the design. Depending on the product and the agreement with the customer the costs may incurred by the customer or shared between the manufacturer and customer. The total cost, in part. influences the customer expectations and satisfaction.
For complex systems, system engineering teams address each of the elements of the life cycle and include reliability analysis as necessary. For simpler systems the burden falls to the design and development teams. In either case the ability to estimate the durability of components and systems allows the design team to make appropriate design decisions that will minimize total cost of ownership.
In some cases the design team may balance the cost of shipping a heavier product that will survive longer with the cost of maintenance of a lighter overall product. As you may imagine there are many possible tradeoffs that permit minimizing life cycle costs. When these costs are estimated and considered during the design process, the ability of the team to optimize life cycle costs increases.
Recommendations
When considering an equipment purchase or an improvement to existing equipment remember the purchase or project costs are only one element of the life cycle costs. In order to make informed decisions may take a little work to understand the cost of downtime, cost of spares, etc. Yet, the ability to consider more than just the intial costs may help you realize significant gains in the future.
Here are a few tips to help you prepare for the total life cycle cost analysis for your next major decision:
- Cost of downtime – gather and track the impact of a ‘line down’ situation. You may need the support of the accounting team.
- Equipment failure rates and failure mechanisms – ask the vendor/supplier for a detailed report on expected failures and necessary spares/maintenance activities.
- Spares ordering times – for expensive items, even if unlikely to fail, how long will the equipment be down before receiving replacement parts?
- Spare storeroom costs – space costs money too, how many spares do you need and how much space will they take, plus consider how long the spares will survive on the shelf (spare rot, too.)
- Technician and tool costs – is there specialized training or tools required to perform maintenance on the equipment. If the only diagnostic tool costs as much as the equipment, is that part of the purchase decision?
Know this information before making a purchase decision. Tailor to the specific equipment and continue to track actual performance and improve your life cycle cost estimates going forward.
With a little work you can avoid those unpleasant surprise costs that may occur over the lifetime of your equipment.
by Fred Schenkelberg
Part 2 of 5 in the Maintenance & Reliability Series
Fred Schenkelberg is an experienced reliability engineering and management consultant with his firm FMS Reliability. His passion is working with teams to create cost-effective reliability programs that solve problems, create durable and reliable products, increase customer satisfaction, and reduce warranty costs. If you enjoyed this articles consider subscribing to the ongoing series at Accendo Reliability.
—
The other articles in the series include:
Post 1 – Incorporating Reliability into Your Future
Post 2 – Using a Design FMEA
Post 3 – Where Does Maintenance Fit Into Reliability?
Post 4 – Life Cycle Costs
Post 5 – Close with Q&A
Leave a Reply