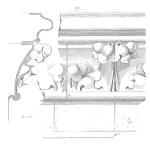
The reality: Savings in work execution can easily be 30 to 60% of what you are spending today! That’s less labor, less overtime, less contracting, less consumption of parts and materials, less spend on delivery logistics, and less procurement activity. If your maintenance costs are in the range of 10 to 30% of your operating spend, you can save 3 to 18% of your operating labor costs by focusing on maintenance planning, scheduling and improving your proactive maintenance program.
The myth: many believe that planning and scheduling will solve their maintenance productivity problems, so they focus efforts to improve them. But despite their efforts, results don’t change. Time and again, we see reports showing relatively high levels of planned work but low schedule compliance, and production outputs don’t change. What’s going on?
From our field experience we know that many planners don’t actually plan – they schedule, and then they chase parts. It’s very inefficient. Of course they are diligently doing their best given what they know and the circumstances they are faced with. However, they don’t know what they don’t know, and they will never be able to correct for a poorly designed maintenance program.
The problems:
- They are not trained in planning. Many planners don’t actually know what planning is. When reporting on % of planned work they are actually reporting on % scheduled, and often the schedule compliance is quite low.
- They are understaffed. In a stable operation a good planner should be able to support upwards of 20 trades or more. If the library of saved job plans is large, then that ratio can be even larger.
- Coordination among trades, even for planned work, is sadly lacking. Planners often have a trade background so they are good at one trade and know a little bit about others. If they are planning for one area (all trades) those plans will be lacking in detail for the “other” trades. If they are planning for a shop, then coordination among the various shops is often lacking because there’s seldom a coordinator role.
- Good job plans take time to build. Creating that big library of saved job plans is a huge task.
- Poorly designed proactive maintenance programs. If you are not preventing what can be prevented, nor predicting what’s coming (and acting on it). Often predicting is done, but follow up isn’t. You get stuck in a break-then-fix cycle. Your planners become parts’ chasers, not planners. No amount of planning and scheduling can fix this.
Considering that planned and scheduled work, executed on schedule, is far less expensive than unplanned, unscheduled and breakdown work, there’s a strong business case for improving that situation. So how do we fix it. Let’s look at each of those problems in turn.
- Training is easily addressed – it just requires a willingness to provide it. Once trained, the planners will know what they didn’t know and be far more capable of doing their job properly – if the circumstances permit it.
- Finding more planners will be challenging. If you want them to come from the trades you’ll need to replace experienced trades with new hires. You’ll be loosing skilled talent and it’s incredibly difficult to replace these days. That’s a huge problem also. The best solution is to increase planning efficiency (get more from your existing staff) – but how? More on that below …
- If you planners have trades backgrounds you are likely to have coordination problems and trades efficiency (wrench time) won’t improve as much as it could. Field supervisors will need to be very cooperative with each other in shuffling trades around at the right times to compensate. This can probably be handled with your existing staffing if it’s not overly lean.
- Creating that library of standard jobs is a huge hurdle and if you are understaffed or undertrained (problems 1 and 2), progress will be slow, and quality may not be ideal, so you’ll struggle for years to build it. That’s probably going to take too long. Again, planning efficiency is the key … more below.
- An ineffective proactive program is something that your planners cannot solve. This requires a concerted effort to review and develop the right PMs and planners rarely have the knowledge nor the capacity to do this. You need Reliability Centered Maintenance for critical assets’, and you need RCM training for those who will do PM Optimization on the remainder of your non-critical assets.
The problems can be solve with a combination of three solutions – training being common to both of the other two.
#5 describes what’s needed. You will need some training in RCM, a willingness to perform the analysis and then execute its decisions, expert facilitation (give up on the idea of doing this yourself – at least initially), and you’ll probably need some engineering talent (it can be relatively inexperienced) working with experienced trades and operators. The problem of poorly designed maintenance programs is wide-spread, but it can be somewhat challenging to identify. Talk to us about how to spot it, and then what to do about it. Contact us here.
For planning efficiency we need to compensate for both a lack of knowledge (training), and a lack of capacity. Training is a small investment to make. To solve the capacity problem, hiring is the traditional answer, but it’s expensive these days, and we are In a tight labor market. Moving people from trades to planning roles exacerbates a problem you already have – finding skilled trades. You might get lucky, or you might consider using junior engineers in planning roles – they are easier to find. That can work very well too, but that could also be quite disruptive to how your organization is structured.
So, here’s another idea – enhance planner productivity with an AI enabled planning support tool.
Fortunately technology is at a point where it can help us with this one. We are collaborating with a data analytics firm to develop a tool that will create high quality, draft maintenance job plans in mere seconds, as opposed to days (the manual way). The plans will require planner review, but it’s far less effort than starting with a blank screen. It can be used to rapidly build that library of saved standard jobs. It won’t take planner jobs away, but it will make them far more productive.
That tool is already in advanced stages of development, and it is already producing results. It will soon be available for Beta testing in the field, and then deployment in basic, premium, and enterprise variants. We believe it will disrupt the planning “world” as it is today, greatly enhance planner productivity, the quality of job plans, and it is coming soon.
If you are interested in being involved in our Beta-testing, please let us know. If you want updates on our progress towards a launch, then let us know. You can contact us by clicking here.
Leave a Reply