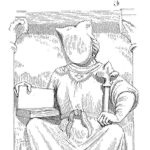
Every once in a while I see a comment that by following the HALT methodology you will “over design” a product.
Many question at what point or operational limit do you quit increasing the stress-strength margins. Those who hold this view of HALT do not understand the essence of what was Gregg Hobbs’ principles and paradigm shift.
The point of HALT is to create the most robust design using standard materials and manufacturing methods.
Reliability development engineers that have applied HALT to electronic circuit boards have probably observed the same, some circuits and assemblies have significant capability.
Many products achieve what Gregg Hobbs referred to as the “fundamental limit of technology” or FLT. That is the strength margins are as large as they can be made without resorting to special materials or designs.
Adding liquid cooling to an air cooled product might be an example of a special method to extend the high temperature operating limit of a circuit or component. Changing a design from being air cooled to liquid cooled, which would most likely add significant costs, due to a thermal limit found in HALT is in most cases not cost effective nor necessary.
Changing a single component found to be a limiting component to a higher voltage or faster switching speed to increase thermal margins due to a low margin found in HALT is the better approach.
Consider each limit and the cost and time required to improve it with each discovery in HALT.
Small Change can result in large Gains in Operational Limits
I have performed HALT evaluations that by changing one component, increasing the wattage from an eighth-watt diode to a quarter watt diode, increased thermal margins by 30°C or more. Sometimes in a change in software that increases a thermal limit.
Most of the time, a change in the value of one or two components found to be limiting a thermal margin is cost effective for creating a more robust system.
For mechanical weaknesses found in HALT, an extra tie-wrap hold a component or repositioning of a component may only be required to result in an increase in vibration strength. Rarely is there a need for significant changes to a design to increase the strength of an assembly to meet or be near the FLT.
To paraphrase what came to me as Gregg’s core belief when he developed HALT methods was:
Start with the frame of reference of the inherent empirical stress-strength that is already in electronics and electromechanical systems built with standard materials and technologies. Use that strength to develop the best ROI screens through HASS (Highly Accelerated Stress Screens)
HALT is also “Highly Adaptive” to each industry
Standard materials and methods may be different for different industries.
Standard materials for electronics systems used in a normal terrestrial environment would include lead-free solder (which has a higher reflow temperature than previous standard lead solders). HALT failures or limits for common environment products is due to reflow of solder (210°C or so) would be in most cases a HALT limit that is not relevant to the field.
Most likely the product will have an operational limit long before reaching a solder reflow temperature. Insulation melting on an electrical connector would also likely be irrelevant to the field in most HALTs.
Yet, In the Oil and Gas downhole MWD (measurement while drilling) equipment design and manufacturing, reflow of solder at 210°C would likely be a very relevant failure, as the designed product operation specification may be as high as 190°C. The product must have some strength (temperature) margin to ensure durability over its lifetime with potential variations in assembly strength and variations use environments.
Equipment failures that stop an oil or gas well drilling operation are very costly and using 300°C solders to ensure a strength reliability margin in MWD equipment is a good standard design requirement for these applications. Using 300°C solders for consumer products for use in terrestrial environments would be in most cases unnecessary over-design.
When HALT has been used as standard reliability development tool for several products, there will be expectations of strength limits for a new product HALT.
Thermal and vibration limits found in HALT for predecessor fielded reliable products can be the benchmark limits for the same types of assemblies (Fans, circuit boards, displays, batteries, power supplies).
HALT does not mandate a change in the product to increase its thermal or mechanical strength. Even the weakest link in a product may be at the FLT.
All HALT results do not require increasing strength limits
Again the key is not designing for HALT, but to design products using lessons learned from predecessor products, using industry standard materials and manufacturing methods, and then finding the weakest link in the design.
The strength of the new product’s “weakest link” may actually be at the fundamental limit of technology, and therefore no improvement necessary.
Related:
A Brief Introduction to HALT (article)
4 Steps to Accomplish HALT (article)
When to Conduct HALT (article)
Leave a Reply