
Establish a Clear Trigger Mechanism
Foundation
After the sponsorship and training are in place and resourcing is defined, there is still no guarantee that any investigations will get done. (See the end of the article for links to the blogs about these needs) This is where the definition of insanity applies – “doing the same thing over and over – and expecting different results” – so something must change. If there is no reason to perform an investigation, then things will continue to happen as they always have. If this is the way you want things to be, then no action is necessary. This is where different way of thinking must truly come into play to counteract the status quo. Time needs to be spent to develop a trigger system that will initiate the analysis, as well as a trigger a system of review and verification that the actions will be followed through. A sample trigger system might look something like the example shown in Figure 1 below:

Adjust Trigger Regularly
It is important to realize that the system above is generic and encompasses many different issues that may plague a facility. The actual triggers should be adjusted to combat the items that are most significant to the facility. We must also be aware that spending a lot of time identifying what to work on may be counterproductive. People can spend weeks collecting data to identify where to apply their problem solving, but during that time, could have fixed multiple immediate problems. This immediate method is mostly applicable to an area, department, or plant that is in a reactive mode and is being bombarded with multiple repetitive problems. So be cautious about falling into “analysis paralysis” by getting bogged down with data collecting if the building is on fire!
What is a team?
Another function of this flow process should be to define the “team.” Notice in the flow that one of the boxes is labelled “assemble RCA team.” In your process definition, you should take the time to categorize the type of RCA necessary. What this means is that not every RCA needs a large formal team to provide a report. Some may only need one person, or a small team, to document the RCA but doesn’t issue a formal report. Some clients have defined this as low, medium, or high intensity, and it is usually driven by the perceived consequence of the problem. In using this format there is also nothing that prevents an individual event from moving from one level to the next after more information is obtained.
Modified Trigger

If you are in a crisis mode, the model in figure 1 can be shortened considerably. The modified version shown in Figure 2 is based on the same concept as above. It has been simplified to show that not all Root Cause Analysis must be done in a large group environment with many people involved. Granted, it is always good to get others involved to review the work, provide alternate viewpoints, or at least ask some pointed questions, regardless of the size of the team. This modified version is also based on significance, or what is most important at the current time. One criteria of a good solution are ease of implementation and certainly the fewer people involved, the easier something is to implement. Many times in an industrial environment, the risk associated with an incorrect analysis is low in comparison to other factors, so speed of implementation is very important.
In either system, the trick is to continually adjust your trigger mechanism to force you to continue to solve problems. In a reactive environment, it may be hard to imagine that you would have to lower your trigger to force yourself to do more analyses, but if you are continually fixing problems, it will happen. The setting of a trigger is one of the most important aspects of a Root Cause Investigation program, and Figure 1 and 2 give some guidelines on how to set them up. One simple method used was to base it on production output or loss, on a time basis, such as daily, shift, hour or some other time-based method. If the production is lower than your trigger set point, then kick off the process and do an investigation. Let the significance drive the number of people and time involvement of the overall investigation.
What is a trigger?
Be aware that there are many types of triggers. One I personally used was a radio tuned to the department frequency that I was responsible for. I would monitor the radio conversation, and listen for things like “production was stopped,” or “some major process piece of equipment was broken,” or anything that I knew would cause them lost production in the short-term. When I heard that, I stopped what I was doing and headed to the area and started my RCA immediately. I wasn’t there to restore production, but I was there to identify underlying causes that I may be able to fix, which would be beneficial to eliminate the problem or similar problems. I left restoring the flow to the maintenance Tarzan’s that showed up, and got fulfillment from getting them back up and running. This was necessary, but I always found it interesting that they never seem concerned with why something failed. During this process, I found things like incorrect parts used, PM’s not done in a sufficient or timely manner, repair work that had been requested and not performed, operator errors, etc.
Lessons Learned
- The definition of insanity is alive and well today
- To effect change, something must be changed
- If you run out of problems to solve – you need to adjust your triggers.
- Not everything needs a big formal team and report
- Focus on what you can do vs what you can’t do
Other blogs in this series:
Introduction to the Essential Characteristics of an RCA Program
Characteristic 1 – Committed Sponsor
Characteristic 2 – A Plan to Provide Program Resources
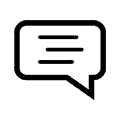
Leave a Reply