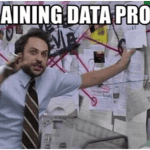
Ernst Hjalmar Waloddi Weibull (18 June 1887 – 12 October 1979) was a Swedish engineer, scientist, and mathematician. (source Wikipedia)
[Read more…]Your Reliability Engineering Professional Development Site
by Semion Gengrinovich Leave a Comment
Ernst Hjalmar Waloddi Weibull (18 June 1887 – 12 October 1979) was a Swedish engineer, scientist, and mathematician. (source Wikipedia)
[Read more…]by Semion Gengrinovich Leave a Comment
The history of Design of Experiments (D.O.E) can be traced back to the work of various individuals, including Genichi Taguchi, a Japanese engineer and statistician. Taguchi made significant contributions to the field, particularly in the area of robust design, which aimed to improve the quality of products and processes. His work was influenced by the need for quality improvement in post-World War II Japan. Taguchi’s methodology, known as the Taguchi methods, was based on the concept of “robust parameter design,” which aimed to make processes and products insensitive to environmental factors or other variables that were difficult to control.
[Read more…]by Hemant Urdhwareshe 1 Comment
This is our first video on ALT in a series of videos on this important topic in reliability engineering. In this video, Hemant Urdhwareshe has introduced basic concepts of ALT. In our subsequent videos on ALT, we will do a more detailed discussion on mathematical treatment, selection of appropriate model and statistical distribution. We will explain these with application example on Minitab software. Hemant is a Fellow of ASQ and is ASQ CRE, CMBB, CSSBB, CQE and CMQ/OE. We are sure that viewers will find it useful.
[Read more…]by Nancy Regan Leave a Comment
Have you ever tried to implement any asset improvement activity but it didn’t go so well? Couldn’t rally the troops? Couldn’t get the kind of management buy-in that you really needed to get things off the ground? If so, you’re not alone.
I’ve read too many articles describing that up to 70% of asset improvement initiatives fail. And I think it’s because a lot of people don’t have a basic understanding of maintenance and reliability principles. So they don’t understand why “change” needs to take place.
[Read more…]by Semion Gengrinovich Leave a Comment
And again there is no one answer for such simple question. Strongly depends on what type of test you need to conduct.
It is also very important to understand at which stage, design of the product. Usually at very early stages of the design there is many unexpected failures, when design is mature enough – failures become predictable, and there is one last period, called – wear out/aging stage.
[Read more…]by Mike Sondalini Leave a Comment
Focus on failure elimination, otherwise equipment failures never stop because they are forever being introduced and perpetuated by poor procedures and practices, poor quality control and poor business management systems.
Knowing defects cause future equipment failures, production downtime, unnecessary costs and lost profits, it is necessary to put defect elimination strategies into place to purposely stop defects occurring and to remove the defects that are already present.
[Read more…]by Hemant Urdhwareshe Leave a Comment
We are happy to release this video on Lognormal Distribution which is a popular distribution to model failures of non-repairable items. In this video, Hemant Urdhwareshe has explained basic concepts of lognormal distribution and its application examples. Hemant also explains its mathematical relationships to calculate MTTF, standard deviation and other parameters In addition, in the video, Hemant has illustrated how to use Minitab and Excel to visualise Lognormal Distribution. Hemant is a Fellow of ASQ and is ASQ CRE, CMBB, CSSBB, CQE and CMQ/OE. We are sure that viewers will find it useful.
[Read more…]by Mike Sondalini Leave a Comment
Plant and equipment failures are business process failures. Plant stoppages and breakdowns result from failure-causing practices built into business processes and from leaving the right reliability practices out of them. Processes may superficially look okay because they have documentation, charts and records, but if you suffer a steady stream of failures, problems, and rework, then your processes contain unforeseen ‘traps’ into which your people and equipment regularly fall. Failure was not intended when your processes were chosen and designed, but failure is what happens when they are used.
[Read more…]by Hemant Urdhwareshe Leave a Comment
In this video, Hemant Urdhwareshe explains how to estimate tolerance interval at given confidence level and specified percentage of distribution. The purpose of tolerance intervals is to assure that the tolerance limits specified during design are achievable during production! Often, the designers specify tolerance limits that are not demonstrated and create lot of rework and/or rejection during production phase. This can increase cost of poor quality (COPQ) and result in redesign of the product and/or revising specifications after the product is released for production. Changes made after product launch can be expensive
I am adding a small correction: at 7:01 minute, please read the tolerance interval as 152 to 308, (and not 358 as shown in the footer).
[Read more…]by Nancy Regan Leave a Comment
Air, sea, space, land, or underground? Commercial, government, or military? Reliability Centered Maintenance has something for everyone!
Absolutely. In fact, in Stanley Nowlan and Howard Heap’s book on RCM, they state:
The content of scheduled-maintenance programs developed by experienced practitioners of MSG-2 techniques may be quite similar to the programs resulting from RCM analysis, but the RCM approach is more rigorous, and there should be much more confidence in its outcome. The RCM technique can also be learned more quickly and is more readily applicable to complex equipment other than transport aircraft.
[Read more…]by Mike Sondalini Leave a Comment
Companies that want plant and equipment reliability need to engage the people in the workplace and give them a large degree of responsibility for improving the performance of their equipment. The most successful solution yet discovered to do that is the autonomous work team.
[Read more…]by Hemant Urdhwareshe Leave a Comment
In this video, Hemant Urdhwareshe explains concept of Confidence Intervals for Mean Time Between Failures (MTBF). The concept is explained for time terminated and failure terminated tests. The calculation is illustrated with Chi-square distribution tables and also Excel Template created by IoQR. The video would be useful to those who want to learn these concepts and learn how to calculate MTBF confidence intervals using tables. It will be beneficial to those who wish to take ASQ CRE, CQE, Six Sigma Black Belt and CMBB certification exams.
[Read more…]by Mike Sondalini Leave a Comment
The world needs plant and equipment that are reliable and fault-free for decades. Yet Maintenance can only keep machinery working by replacing broken and at risk parts. Even industrial asset management only aims to lower the cost of plant and equipment ownership. Neither methodology has the capability to deliver what mankind needs in future. Before the end of this century both disciplines will die-out because intelligent production machines will be made that are completely reliable and maintenance-free for their entire lifetimes.
[Read more…]A Business Case Evaluation (BCE) is a decision-making tool that assists in making value-based funding decisions. Business cases are developed in the early capital and operating budget planning cycles as a standardized and systematic process to analyze the benefits and costs of various options to solve an identified problem or a cost-saving/revenue-generating idea. A big part of building better business cases is analyzing the system over the long term for monetary and non-monetary aspects. Building better business cases improves reliability and performance by formally documenting “needs” versus “wants.” Business cases serve as a powerful communication tool at all levels of an organization. [Read more…]