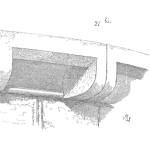
A longer video from Nancy with an introduction to the reliability centered maintenance, proactive maintenance, plus the anatomy of a well-planned RCM program.
[Read more…]Your Reliability Engineering Professional Development Site
A listing in reverse chronological order of these article series:
A longer video from Nancy with an introduction to the reliability centered maintenance, proactive maintenance, plus the anatomy of a well-planned RCM program.
[Read more…]by Miguel Pengel Leave a Comment
Optimum replacement time – Theory
The optimal asset replacement time calculation has one goal, and that is to calculate the lifetime of when assets should be operational as to have the lowest possible operating cost over its lifetime.
This means balancing two opposing forces, namely the increasing operational cost and unreliability of the asset as it ages, with the decreasing effective cost of ownership. [Read more…]
by Mike Sondalini Leave a Comment
Discover 15 ways to operate so there is less maintenance, fewer maintenance people, lower maintenance costs and (because there is less maintenance) your plant runs reliably for longer! Most of the 15 topics covered are new to operations and maintenance. Each one reduces downtime, save money and improves operating uptime and performance.
by George Williams Leave a Comment
George Williams, Founder and CEO of ReliabilityX, discusses how Weekly Scheduling helps drive improvement in the efficiency of the maintenance organization! Have any questions? Drop a comment below!
[Read more…]by Mike Sondalini Leave a Comment
An endless Dilemma confronts every business. It is how to ensure that the activities we undertake will always produce the intended results.
Explosions, workplace deaths, harmful accidents, physical injuries, damaged goods, scrapped jobs, repeat work, manufacturing errors, operating mistakes, bad repairs, misunderstanding, wrong decisions, supplier miscommunication and poor delivery performance are all examples of the many unwanted troubles and problems caused by the Dilemma. Its impacts and effects have been written about for more than 6,000 years of recorded human history.
The Dilemma’s prevalence throughout the world indicates that human beings are a major contributor. A second major factor is business design: how your processes are configured and operate determines your degree of success in addressing the Dilemma. A third big cause is our training and education processes which have transferred the Dilemma all through businesses and across cultures for over 60 centuries. To stop the Dilemma affecting your company you can use what we have learnt about the universe, people and business processes during the last 100 years.
[Read more…]by Nancy Regan Leave a Comment
In this video we touch on all 7 steps of the RCM process as we introduce one of the most important aspects of the application of RCM…asking the people who really know!
[Read more…]by André-Michel Ferrari 2 Comments
I have often heard employees complain they have no data to initiate a proper Reliability Improvement Program. This is not always true. And to no fault of theirs. They just don’t know how to use what they already have in terms of records. If you are running an operation, you should at least have production records – i.e. how much you are producing on a daily basis. If you don’t have this, then maybe you should not be in business at all. This article looks at ways to initiate a Reliability Program using the Barringer Process Reliability (BPR) methodology. The greatest advantage of this methodology is that it only requires productions records as an input. That is how many units of production the plant produces on a daily basis. For example, the barrels of crude oil processed per day in a refinery. Or the hectoliters of beer brewed in a brewery daily.
[Read more…]by Lindsay Walker Leave a Comment
In the intricate landscape of modern manufacturing, the efficiency and quality of the production system are paramount. These two pillars underpin a company’s competitiveness, profitability, and customer satisfaction. A critical factor influencing these metrics is the maintenance strategy employed. This research delves into the profound impact of maintenance strategies on production efficiency and quality, exploring various approaches, their implications, and real-world case studies.
by Mike Sondalini Leave a Comment
Many managers think that high equipment reliability needs a reliability mindset. They think you need the right beliefs and values to get reliability. Reliability requires both correct thinking and correct behaviour, but behaviour is by far the most important. Your plant and machinery will deliver outstanding reliability only if their parts are not heavily stressed. Reliability is the result of properly doing the right actions to the parts in your machines—the right belief comes later, once the evidence is in. You make your machines and equipment reliable; you do not think them into being reliable with a good attitude. You do not need to have the right mindset to get highly reliable machines; you only need to deliver to your machinery parts the right environment for high reliability. If reliability is mostly the result of the behaviours that you do, it means that great reliability can be created everywhere.
[Read more…]by George Williams Leave a Comment
In this video, George discusses how clean, dry, well balanced, and consistent air can be a huge opportunity for continuous improvement in a facility. If you’re looking to improve the efficiency and reliability of your facility, you won’t want to miss this!
[Read more…]by Mike Sondalini Leave a Comment
Value Driven Maintenance is a financial modelling method to pick maintenance process improvements. Used alone VDM gives you a “starry-eyed” view of maintenance savings. Once you combine VDM with Plant Wellness Way system-of-reliability analysis you get practical solutions.
[Read more…]by Nancy Regan Leave a Comment
I have a service that regularly monitors my home for termites. Using RCM, let’s determine if this Condition Based Maintenance task is both technically appropriate and worth doing.
[Read more…]by Mike Sondalini Leave a Comment
A definition: Maintenance describes the management, control, execution and quality of those activities which will reasonably ensure that design levels of availability and performance of assets are achieved in order to meet business objectives. [Read more…]
by George Williams Leave a Comment
Today we are going to look at Design Rates. Often times our equipment are not running at their designed rate. Most of which are operational issues. For example, we tend to slow down a line, to present less problems, but it lowers the target rate. How do we identify an actual opportunity?
[Read more…]by André-Michel Ferrari 2 Comments
In his book Reliability Centered Maintenance1, John Moubray highlights 6 patterns of failure. However, one needs to be careful about how those patterns are interpreted and used. Or misused. These 6 failure patterns are as follows: