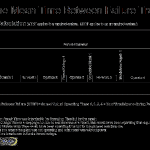
An MTBF calculation is often done to generate an indicator of plant and equipment reliability. An MTBF value is the average time between failures. There are serious dangers with the use of MTBF that need to be addressed when you do an MTBF calculation.
Take a look at the diagram below representing a period in the life of an imaginary production line. What is the MTBF formula to use for the period of interest to represent the production line’s reliability over that time? [Read more…]