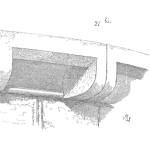
The Importance of Having, Setting, and Living Values as a Leader
Leadership is not just about making decisions or achieving results—it’s about setting an example and guiding others toward a common purpose. One of the most powerful ways a leader can do this is by having, setting, and living values that resonate with both themselves and their team. Values are the principles and beliefs that guide actions, shape behaviors, and define the culture of an organization. For leaders in any field, including maintenance and operations, these values become the foundation upon which everything else is built. In the context of Leadership Values in Maintenance and Operations, this foundation is especially critical, as it ensures safety, reliability, and collaboration in high-stakes environments.
[Read more…]