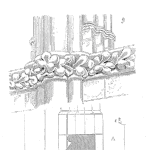
A point estimate of the mean of a population is determined by calculating the mean of a sample drawn from the population. The calculation of the mean is the sum of all sample values divided by the number of values. [Read more…]
Your Reliability Engineering Professional Development Site
Prep notes for ASQ Certified Reliability Engineer exam ISSN 2165-8633
The CRE Preparation Notes series provides you with short practical tutorials on all the elements that make up the ASQ CRE body of knowledge. The articles provide introductory material, basics, how-tos, examples, and practical use guidance for the full range of reliability engineering concepts, terms, tools, and practices.
Keep your knowledge fresh by regularly reviewing topics and tools that make up reliability engineering.
Sign up for the CRE Preparation Notes email list for the new reliability engineering short tutorials.
- Improve your reliability engineering skills
- Learn about the wide range of tools available
- Enhance your resume with the ASQ CRE
You will find the most recent tutorials in reverse chronological order below.
by Fred Schenkelberg 2 Comments
A point estimate of the mean of a population is determined by calculating the mean of a sample drawn from the population. The calculation of the mean is the sum of all sample values divided by the number of values. [Read more…]
by Fred Schenkelberg 2 Comments
The basic measures of central tendency are mean, median, and mode.
Given a collection of data, a common question is about where the data resides. Knowing the center or mid-point or average is a starting point as we consider the data. [Read more…]
by Fred Schenkelberg 21 Comments
It may be possible to pass the CRE exam knowing one formula.
The math elements of the exam may take a bit of time to solve, and knowing reliability statistics well is a good plan heading into the exam. Knowing the exponential distribution reliability function is one that you should memorize. [Read more…]
by Fred Schenkelberg 4 Comments
Preventive Maintenance or PM is a set of inspections and tasks that help prevent equipment from failing. Keeping equipment operating improves plant capacity and throughput. Avoiding unwanted downtime helps the plant avoid unnecessary expenses and lost productivity.
Checking the oil level in your car’s engine and adding more as needed, along with regular oil changes are examples of PMs. [Read more…]
by Fred Schenkelberg Leave a Comment
A reliability block diagram is a graphical and mathematical model of the elements of a system permitting the calculation of system reliability given the reliability of the elements.
The model reflects the reliability performance structure including series, parallel, standby and other arrangements of system elements.
Each block in an RBD represents a component or subsystem of the system. The organization and connecting lines represent the reliability structure of the system and may or may not be representative of the system’s functional block diagram. [Read more…]
by Fred Schenkelberg Leave a Comment
A simple assumption in many experiments is to assume the variable act independently on the response.
This means when I change the temperature a little in a polymer dryer silo that time to achieve a certain dryness goes down. And, changing the humidity or airflow rate or pressure either do not change or as they change has no impact on the relationship between temperature and drying time. [Read more…]
by Fred Schenkelberg 2 Comments
The purchase price of a product may be the start of the cost of ownership.
Maintenance and repairs may cost many times the initial purchase price. An efficient maintenance process and low-cost spare parts may help minimize cost, yet a design that optimizes the total cost of ownership is the most effective method. [Read more…]
by Fred Schenkelberg 1 Comment
Dr. Nelson created a simple experiment to illustrate the effect of meddling with a stable process. (Dr. Deming did something similar)
While the intent of making small changes to a process may be to make improvements, these perturbations generally increase the variation of the results.
To improve a process requires understanding the source of the variation and often controlled experiments to identify process improvements. [Read more…]
by Fred Schenkelberg Leave a Comment
For those that sat for the exam last Saturday – how did it go? what surprised you or confused you? Was your preparation adequate?
Cheers,
Fred
by Fred Schenkelberg 2 Comments
Another variation of the X-bar and R chart, in this case measuring and plotting individual readings instead of a sample average. The range value is obtained from the current reading and a fixed number of previous readings.
This type of control chart is suitable for calibration or testing situations where it is not practical to create subgroups of items for samples. [Read more…]
by Fred Schenkelberg Leave a Comment
The s chart replaces the R chart and provides an increase in sensitivity to variation of the spread of the data.
The s-chart works better with 10 or more items per sample in order to obtain the s (standard deviation) estimate. The use of a spreadsheet or calculator expedites the calculation of the sample standard deviation.
by Fred Schenkelberg 2 Comments
Control charts provide an ongoing statistical test to determine if the recent set of readings represents convincing evidence that a process has changed or not from an established stable average.
The test also checks the sample to sample variation to determine if the variation is within the established stable range. A stable process is predictable and a control chart provides the evidence that a process is stable or not.
Some control charts use a sample of items for each measurement. The sample average values tend to be normally distributed allowing straightforward construction and interpretation of the control charts. The center line of a chart is the process average. The control limits are generally set at plus or minus three standard deviations (of the sample means – commonly called the sampling error of the mean) from the grand average.
by Fred Schenkelberg Leave a Comment
Every process should operate stably. Every process may have many measurements available to monitor either various aspects to the final product or the assembly equipment. There may be hundreds of possible items to measure and monitor.
We do not have the resources nor time to apply control chart principles to each possible measurement. Control charts do not directly add value and they have a cost to maintain and interpret. While it may be tempting to add a dozen or so control charts, as the cost increases the value quickly decreases.
by Fred Schenkelberg 3 Comments
As stated before, variation happens.
The root cause of the variation for a stable process includes material, environmental, equipment, and so on, changes that occur during the process. No saw cuts the same length of material twice – look close enough there is some difference. [Read more…]
by Fred Schenkelberg 4 Comments
An easy method to monitor and control a process average. It is an alternative to the Shewhart control chart.
Pre-control charts work well with stable and slow process drifts or changes. These charts provide a means to monitor a process and act as a guide for process centering.
They are easier to setup, implement, and interpret the Shewhart charts. [Read more…]