
Guest post by Ken Latino
If you are like most people who work in a manufacturing or process plant, you have a plan for your day when you arrive in the morning. As soon as you walk through the gate, you are hit with the equipment failures from the night before. You immediately spring into action to help find parts, drawings, millwrights, fitters and anything else needed to get the equipment repaired as quickly as possible. Once that is underway you are told to compile that urgent report for corporate that is needed immediately. And who can forget the countless meetings that must have your attendance. The next thing you know, it is 7:00 PM and you have done nothing from the plan you had for your day. Sound familiar?
This is typical in a busy plant environment. There is always more work to do then there are hours in the day. Unfortunately, the reactive work is the work that gets the highest priority. If you have a critical piece of equipment down, you are not likely to run that PM or work with a team on the RCM project. The fact is reactive work is always seen as more urgent than proactive work. Reactive work must be done NOW while proactive work can always be pushed to another day.
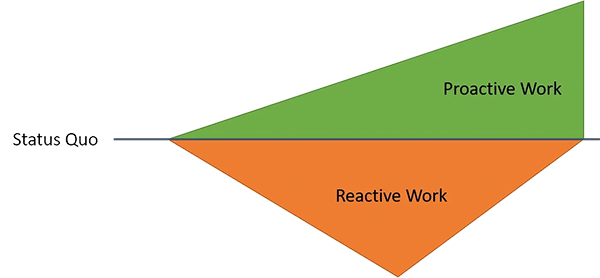
The problem is that working on reactive work never really moves us forward. We are maintaining the status quo at best. So how do we make proactive work a priority with all the reactive work we are required to do?
While there is no simple answer to this question, there are some effective strategies you can employ to help. Step 1 is you need organizational consensus that reactive work does not improve the status quo and only proactive work will drive improvement and productivity. The next step is to determine what proactive activities can help improve the facility.
There are a variety of proactive strategies that could be employed to drive improvement. There are too many to name in this short article. However, some of the most practical ones that come to mind are:
Develop Equipment Strategies (Strategize)
- Define Critical Systems
- Determine Failure Modes
- Determine Risks (probability x consequence)
- Develop mitigating actions for risks
Work Management (Execute)
- Work Identification (e.g., operator rounds)
- Prioritize the work (includes preventive, predictive and other failure findings activities)
- Plan
- Schedule
- Execute
- Document and Follow Up
Failure Elimination (Evaluate)
- Identify Repetitive Failures
- Prioritize by Impact to the Facility
- Perform Root Cause Analysis (RCA)
- Ensure Corrective Actions are Implemented
- Modify and Enhance Equipment Strategies
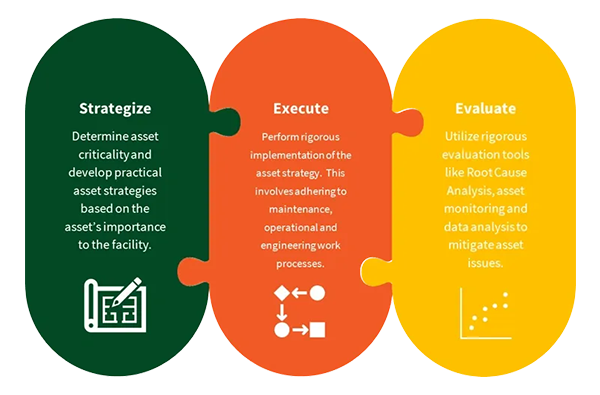
I think of this as Strategize, Execute and Evaluate. Build a strategy for your equipment, execute that strategy and then evaluate whether it is effective. For this to really work it must have a foundation of support from both senior and plant management. This means that we have commitment from leadership to dedicate some of the plant’s limited resources to proactive efforts. People need to have defined roles and responsibilities and have the training and tools necessary to perform the proactive work.
I am not suggesting that every plant resource needs to be dedicated to this effort. That is not practical, and it will not work. However, we can dedicate just a few key resources to driving these efforts. This means we do not pull these resources to fix the “failure of the day”. These dedicated resources will, over time, slow the vicious cycle of reaction and ultimately begin the virtuous cycle of proaction. Each proactive activity will build upon the last creating more time and more resources that were previously inundated with reactive work.
I cannot stress enough the importance of making proactive work, PRACTICAL. If the work is not practical, it simply will not be accepted into the day-to-day activities of the plant. Think of this transition from reaction to proaction as evolution rather than revolution. Be patient and persistent because reaction is a very difficult habit to break! But in the long run, the rewards far out way the investment. Reliability is one of the few investments you can make that will positively impact every aspect of a facility. Safety, Environmental, Cost, Availability, Employee Engagement and EBITDA.
As always, I welcome your feedback and ideas that will promote reliability improvement.
Leave a Reply