
This is our third article about the 3 ways to do reliability allocation. In the first article, we set the scene. We talked about the reliability design cycle that needs to be implemented to make sure what we do will actually work. Will actually matter. In the second article, we cover the six steps of reliability allocation. In this article, we go through the six steps of reliability allocation.
You should have already read these articles – and if you haven’t please do! Once we have our reliability design cycle up and running, there are six key steps to making reliability allocation happen. And this article is about the sixth step – doing something!
If you want to learn more about a straightforward approach to reliability allocation – read this!
Lets recap
This article is a little shorter than the others (… hooray I hear you all say). But it is no less important than the others. Because this is the article that covers what options you have as a design team leader when you realize which of your components are not on track to meet their allocated goals.
Remember our reliability design cycle that starts with reliability allocation, then goes through design, updating system reliability models, identifying the ‘vital few’ ways your system will fail, simulation, analyzing, testing, re-estimating system reliability and working out if you are there yet?
Go through all that, and then decide to do something. If any of your components aren’t on track to meet their goals, then you don’t just admire that problem. You don’t berate the team that is having issues. That won’t improve anything. Nor is it leadership.
So what can you do if some components aren’t on track to meet their allocated reliability goals? Here are some suggestions.
Doing something #1 – (Re)allocate reliability from a component that is ‘doing well.’
Once you have gone through a design iteration or two, you should have a system reliability model. So your simulation and analysis (noting that testing may come later in the design process) should help you work out which component is on track to meet or even exceed their allocated reliability design goals. If your power supply design team is doing really well, you can increase their allocated reliability goal.
Why? Because this allows you to lower the reliability goal allocated to any component that is struggling to meet its original goal.
But be careful! Make sure the design team who is doing well doesn’t feel like this is punishment. Don’t make them feel like they simply have reliability allocated ‘away’ from them if they work harder than the rest. They perhaps need to be treated like heroes! Their work and diligence have just given you and the rest of the design team a gift! All design teams should be aspiring to this.
And if you can motivate your design teams to behave in this way – you won’t have to carry out any of the less palatable steps below.
Doing something #2 – Allocate reliability from your design margin
Remember Step 3 in our reliability allocation process that we discussed in our second article?? In our medical device example, we kept 1.1 percent of ‘allocatable reliability’ to yourself as the design leader. This made sure everyone worked aspirationally from the start. There will be challenges in every design process. And if there is no single component that is on track to exceed their allocated goal – then the next thing you can do is give the design teams who are really struggling some of your reliability design margin.
But be careful doing this. Once your reliability design margin is gone – it is gone!
Doing something #3 – Invest more time or money into your struggling components
Obviously we would like to avoid this. But regardless of what we would like to think about even the best design processes, there are so many uncertainties when it comes to budget and schedule that we really shouldn’t be surprised when we underestimate them.
Most projects have contingencies in their budget and schedule. So they should be used if need be.
But the real benefit of investing more time or money into design as part of the reliability design cycle is that you can do this early. A robust process with sound reliability allocation practices mean that you find out about potential problem areas as soon as possible. System reliability models along with targeted simulation and analysis should give you a really good understanding of where you are at. Well before testing.
We often use a ‘factor of ten’ rule when it comes to design. This means that for every design iteration you go through, it becomes ten times more expensive to make a design change. So instead of fighting it, try to understand if you need to invest additional time or money as early as possible. Because if you do, it could be 10 times, 100 times or 1000 times less expensive than doing it later.
Doing something #4 – Consider outsourcing a troublesome component
There are many reasons why we would like to manufacture every part of a product or system. Protection of Intellectual Property (IP). Less import and export control bureaucracy. Less time spent on contract and relationship management.
But there may be third parties or suppliers out there who are just better at making that component than you are. Making that one sensor, alloy or glass tube might be the only thing they do. They may mass-produce it – which typically means that they can control manufacturing quality as well.
So if you one of your design teams is really struggling – look for help outside your organization! And again, looking for this help is much easier when you identify a need for it early.
Doing something #5 – Consider redundancy
Now we think about redundancy. Having more components than you need adds weight, complexity, maintenance liability, heat and lots of other things that you may not want. But – redundant components improve reliability without major technological investment.
So we may want to prioritize which components we consider for redundancy. And reliability allocation helps us get there. The ‘easiest’ component to incorporate redundancy may allow reliability to be allocated to other components as well.
The point is – allocating reliability and following the reliability design cycle makes this thought process easy.
Doing something #6 – Update your business assumptions
And lastly, if we cannot affordably meet our original reliability goals (a conclusion we arrive at only after we have taken the time to thoroughly understand our system) we may be forced to have a look at our business plan. We may have to reduce our warranty period. We may reduce our advertised service life. We may have to increase our support plan.
This is not defeat – this is accepting reality. If, and only if, you have correctly allocated reliability and followed the reliability design cycle thoroughly. And again, accepting reality is much better financially the earlier you do it.
So in our next article …
… we talk about allocation factors! Finally! The numbers we need to come up with to work out what our allocated reliability goals are. These factors are the things we incorporate in Step 5 of reliability allocation – which we talked about in our last article. The reason we have taken so long to start talking about them is that everything else is in a way … much more important. The reliability design cycle is the most important part of making a reliable product. And if you don’t have a robust approach to designing for reliability – all reliability allocation efforts are in vain. So you need to get ready to allocate reliability. You need to understand that you should not exhaustively analyze what you think is analyzable and simply come up with allocation factors that create a starting point for design. They have to be updated and optimized.
So till next time!
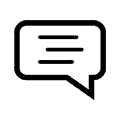
Leave a Reply